What’s right, what’s wrong & what will cause problems
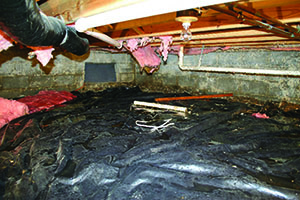
Improving performance & appearance. A vented crawl space (above) often has falling fiberglass insulation and moisture problems.
Builders love crawl space foundations because they’re quick and inexpensive to build. You don’t need heavy equipment to excavate a giant hole for a full basement. Instead, you’re erecting short walls to get the first floor framing up off the ground. If soil at the building site is rocky or wet, a crawl space minimizes the risk involved in digging and building a full basement.
The failure of fluffy stuff
For many years, the standard way to build a crawl space involved venting the crawl space walls and installing fiberglass batt insulation between joists in the crawl space. The widespread availability of fiberglass insulation, along with its low cost, went along well with the other economies of crawl space construction.
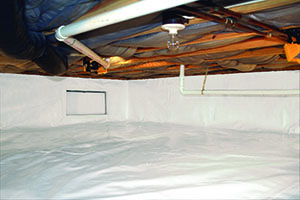
The encapsulation process results in a clean, dry interior space, as shown here.
Unfortunately, the same fluffy batt insulation that works well in wood-framed walls performs miserably in crawl spaces. Here’s how energy expert Martin Holladay describes the disastrous results of installing fiberglass batts in a vented crawl space in a recent blog at GreenBuildingAdvisor.com:
“If you’re perverse, and you want to build a damp, moldy, nasty crawl space, just do two things: insulate the crawl space ceiling with fiberglass batts, and vent the crawl space to the exterior. If you live in the Southeast, within a few short years the fiberglass batts will begin to hang down at odd angles like drunken stalactites. Every summer, the open vents will introduce huge amounts of moisture into the crawl space. You’ll end up with a classic moldy crawl space — one that represents a significant source of moisture for the house above.”
The mold that thrives in a damp crawl space won’t just damage wood and other organic materials in the crawl space. Research has shown that up to 40% of the air we breathe upstairs comes from the basement or crawl space, so the potential for hazardous indoor air pollution (from airborne mold spores) is very high. These are serious problems.

A smarter insulating strategy. Installed against crawl space walls, rigid foam insulation won’t degrade or fall out of place.
The solution: Change the thermal and pressure boundaries
OK, I know this heading may seem a little cryptic, but stay with me. In the old-style vented crawl space, a layer of poor-performing fiberglass insulation is supposed to provide a thermal barrier directly beneath the first floor of your living space. The pressure (air) barrier in a vented crawl space is also the floor sheathing, even though it’s got plenty of holes in it to bring wiring, plumbing and ductwork up through the crawl space.
What happens if we change these pressure and thermal boundaries? Seal the crawl space vents so that moist exterior air can’t get into the crawl space. If the crawl space has a dirt floor, seal that with a thick plastic vapor barrier. Install rigid foam insulation against crawl space walls, so that we’re insulating the crawl space instead of the first floor. The result of this crawl space “encapsulation” process is a clean, dry crawl space that isn’t affected by moisture in the soil or in the outside air. Unlike fiberglass crawl space insulation that can degrade into a pink pile on the crawl space floor, rigid foam insulation can’t absorb moisture or be damaged by it, and will never fall out of place. Any moisture that remains in the wood framing after a crawl space is encapsulated can be effectively removed with a dehumidifier. Once this happens, you’ve got a controlled environment where mold can’t grow, and a crawl space that’s more of an asset to your house than a liability.
You are correct in that a rigid style foam insulation is the best form of insulation to use when trying to seal your crawl spaces, as long as each panel is correctly taped together this can be one of the best ways to essentially vapor lock your crawl space, it stops air, moisture, dust, smells, and is truly a great way to eliminate the above from your home, the johns manville foil board is also a good product to use for this.
This is what want to do to my 1920’s craftsman, but the walls are stone masonary and have and uneven suface. If I run the vapor barrier up to the sill and use fiberglass bats will the vapor barrier stop the batts from geting wet? I know I can go the closed cell spray foam way but I worry about wood rot, or insects on the rim joists that I could not see. Spray foam just to the top of the masonary and use ridig fowam bord on the joist so you can still gain acces to inspect?
Any advice would be great northern NJ.
Avoid using fiberglass batts in the crawl space. Spray foam offers a fast and effective way insulate the uneven surface of a stone foundation wall, but it can get expensive. A good first step would be simply to insulate the rim joist by friction-fitting rigid foam insulation against the rim joist and between floor joists and then sealing around the foam board with 1-part spray foam. It’s also important to seal gaps where the mudsill rests on the top of the foundation. Termites and carpenter ants are unlikely to go after wood that stays dry, so your risk is minimal if you can keep the rim joist area dry. Just by sealing the rim joist you are likely to notice improved comfort and energy efficiency; then you can decide about insulating the stone wall.
Hi Tim I have a cottage in Massachusetts that is supported but only has a cinder block wall half way around it. I am looking for wall options to complete the wall so I can then have insulation added to the wall and then encapsulate.
Kind of like an insulated skirting. Thanks
I have the same problem in that my foundation is stone and uneven. Did you ever find a good solution to insulation your crawlspace?
I understand the foam insulation against the walls but what about the portion of the wall above the cinder block/cement wall between the joists? Should I cut up some of the foam board insulation and fit them into the space? What adhesive should i use to place the foam insulation?
Any tips for sealing the vents?
Yes, it’s VERY important to seal and insulate the rim joist. See the comment above for details on how it’s done. As for sealing the vents, it’s possible to make vent covers from 3/4-in. exterior plywood cut to fit over the vent opening. A foam gasket should be used to seal the edges of the vent to the wood rough opening. Stainless steel machine bolts, driven into threaded inserts installed around the rough opening, will enable you to remove the cover in the future if necessary. To insulate the vent cover, glue some rigid foam insulation against the inside face of the vent cover.
Hi Tim. Thanks for the crawl space insulation tips! I have a few questions for you as I have a slightly unique situation in my house in northeastern PA. The previous owners had expanded the kitchen from the house and installed a crawl space under the new addition. This crawl space is accessible from an existing basement window. For some reason, the builders added crawl space vents. (My understanding is that if the crawl space was opened up to a condition space, – i.e the removed the basement window to open it up to the inside – there really was no need for vents.) I am planning on sealing up the vents and insulating the space per your advice above. If I remove the window and create an open access point the the crawl space, would you recommend installing some sort of vented door hatch or a sealable one? Also…out of curiosity, does foamboard insulation installed in a crawl space require a fire barrier laid over top of it, like drywall? I know it’s required for living spaces like a finished basement, but just curious if building codes have addressed this.
Your wisdom is appreciated!
Assuming that you’ll be able to access the crawl space from the basement window, all vents in the crawl space can be sealed permanently as part of the encapsulation process. Rigid foam board insulation should not require a fire barrier when used in a crawl space. Once the crawl space has been insulated (make sure to air-seal and insulate the rim joist throughout the crawl space, as well as the crawl space walls), there should be no need for an insulated door between basement and crawl space. You may want a door for other reasons –to keep out pests, for example. Good luck.
Hi Tim,
I have enjoyed your comments. I have a situation with a 1930 home in Savannah, Ga. It sits on a above ground 4 ft crawlspace. It has approx 2’x2′ brick pillars spaced around the perimeter with lattice in between. It is not encapsulated, free movement of air. The house is in a flood zone, but the 1st floor sits about 5′ above the base flood elevation. It is not insulated at this time. How would you insulate the floor? I have worked storm claims / flood claims for insurance companies and I have seen my share of wet insulation after a flood. It is important to be able to quickly remove it from the floor to prevent more damage, thus my concern in doing closed cell foam insulation. Thank you for your time and advice.
Savannah is a beautiful city and it sounds like you have an historic house that is worth caring for. The first step in your case would be air-sealing the first floor (crawl space ceiling) with 1-part spray foam (cans of GREAT STUFF). All penetrations for wiring, plumbing and ductwork can be foamed to form an air barrier that will also help keep out insects and other pests. Pier-supported buildings have no foundation walls, so encapsulation isn’t an option. Having 2-part, closed-cell spray foam sprayed between floor joists would accomplish air-sealing and insulation in one step, but (as you mention) it would also trap moisture if a storm surge brings water above the first floor level. A viable alternative would be to fasten sheets of rigid foam (1.5 or 2 in. thick) along the bottom edges of the joists, using screws and large washers. Don’t use EPS (white Expanded Polystyrene) rigid foam; it’s less durable than extruded polystyrene and polyiso foam board and with lower R-value as well. Sealing the seams between panels with tape will improve the air barrier. For odd-sized areas you may need to fill voids around the rigid foam with GREAT STUFF. This treatment will greatly improve comfort and energy efficiency, and it can be taken down if necessary. Good luck.
Tim,
Thank you so much for your advice. You are correct this is a historic home. Couple of questions/clarifications. If I understand your advice correctly–you are saying first use a 1 part spray foam Great Stuff (is this specifically called 1 part?) around all wiring, plumbing, any cracks. Since the house is in a flood zone you aren’t recommending spraying closed cell foam insulation between the joists but as an alternative screw rigid foam insulation to the bottom of the joists taping at the seams. Last week the pipes froze in the crawlspace, would you put the foam tubes over all these pipes as well? Usually freezing isn’t an issue in Savannah, but it was last week with 19 degrees. Thank you again for your advice. Kathy
Kathy:
Up north where frozen pipes are an issue every winter, beach houses built on piers and crawl space houses have a way to protect water lines that extend beneath the house. The rigid foam application (to the bottom of the crawl space joists) should protect water lines that run in the joist space. For the lines that extend lower, into the ground, it’s common practice to build an insulated box that extends from the floor to the ground. Access to the box interior will be necessary –either through a hatch in the first floor, or through an insulated, weatherstripped door in the box. Rigid foam is the preferred insulation to use around the box. As an extra precaution, the water lines can be wrapped with electrical heat tape that will turn on automatically if temperatures drop below freezing.
Tim, Kathy again. Another question: if we use rigid foam insulation screwed to the joists like you suggested, is this going to create a moisture problem between the floor and the foam in this air space? I don’t know if the floors have a sub floor, the floors are the original heart of pine in the house. Thanks.
The potential for a moisture problem will occur on humid summer days. If warm, moist outside air gets past the foam insulation and into the joist space, condensation is likely to occur when this air contacts the underside of the flooring, which will be cooler. To avoid this moisture issue, I suggest doing a good job of sealing the rim joist and the joints between foam insulation boards.
Tim
Thank you so much for all the information.
Kathy
CAN I GLUE THE RIGID INSULATION DIRECTLY TO THE SUBFLOR FROM
CRAWL SPACE?
Hi Tim; I’m replying with Kathy’s question because it’s a related topic.
Am I correct in assuming that Kathy has a wood floor and that this is the reason that she would need to remove the insulation in the event of a flood? We have a similar setup (townhouse in flood plain, on foundation and cement piers, crawlspace under main floor, venting to allow air/water movement between adjacent units) . In our case the crawlspace ceiling is concrete slab supported by iron I-beam. Sewer pipes go through the slab and connect in the crawlspace to a common pipe which travels under all the units to a common exit.
Would it be possible to using closed cell spray foam in this case to insulate under the concrete slab? Or is foam board still the best option so that it can be removed? Is there an issue if spray foam under concrete with pipes going through it gets soaked in a flood?
Also, once insulated do we have to worry about freezing pipes in the crawlspace? Air movement is between our unit in the middle of the block and sideways adjacent units but not to outside cold air (the ground freezes in winter).
Guidance would be much appreciated!!!
Claire: You have several options for improving comfort and cutting your heating costs. Having 2-part, closed-cell spray foam applied to the underside of the concrete crawl space ceiling is one option. Closed-cell foam won’t absorb water, so it should be OK if flood water gets into the crawl space. The same is true for closed-cell foam boards that are applied to the crawl space ceiling. Which option you choose will probably depend on price. Foam board insulation is difficult to install against a surface that isn’t flat and unobstructed. Some folks who are doing interior remodeling over a concrete floor choose to lay down rigid foam board insulation over the concrete and then install underlayment and finish flooring. If you can afford to lose 2.25 in. of headroom in your living space, this insulation treatment will be less costly than crawl space insulation.
As for your concerns about freezing pipes in the crawl space, yes this is certainly a concern. When the crawl space can’t be fully insulated and encapsulated, freeze protection can be achieved by building a “hot box” –an insulated box that surrounds the pipes coming from the ground to the living space. Good luck.
Tim,
This information has been very helpful but I was wondering is it relatively easy for anyone to do? A few months back my husband and I had several companies give us estimates on encapsulation of our crawlspace. The cheapest was $6,700 that was with a sub pump and the stabling of main bean. Do you think we should attempt this project ourselves or have a professional do the work? We really would like to save money but we want it done right so we’re not paying more in the long run anyway. Neither of us have done any real home improvements outside of painting and laying floor tiles.
Making structural repairs (like stabilizing a beam) and installing a sump pump are definitely jobs for pros. Installing the rigid insulation and air-sealing involve techniques that DIYers can accomplish. Because you’re working in a space that’s dark, cramped, dirty and damp, it’s hard work. The good news is that if it’s done right, it only needs to be done once. Good luck.
I have a 1925 log house in Finland (http://villainkeri.com/wp-content/uploads/2014/01/Winter.jpg) that has an earth floor underneath. The conventional wisdom here is that wooden houses need to breath and sealing is not good in the long run. My problem is the floor is typically 50 degrees and room is 68 and our energy consumption keeps creeping up despite the outside temperature being constant (around 6 degrees). I believe as the foundation freezes it’s taking more and more heat to keep the house warm. If I were to condition the crawl space do I put in a vapor barrier by default and if not what are the conditions to consider before putting in a vapor barrier?
It looks to me like your house crawl space needs a full encapsulation treatment with extra rigid foam insulation installed against the foundation walls. It’s worth studying the aspects of encapsulation so that you can be sure the process is completed correctly. You’ll find good information at http://www.basementsystems.com.
Hi Tim,
My situation is similar to Kathy’s. I live in Greenville, SC, and my home is built on piers with an exterior brick facade. I have hardwood floors with 15lb felt between the subfloor and hardwood. The batt insulation underneath is old and falling out and the duct work needs replacing as well. My thought is to do what you suggested for Kathy after I have new ducts installed. So, do I have to remove old insulation? Do you think I could be creating a moisture problem that would effect the hardwood flooring?
Hi Roy,
I would definitely remove the old fiberglass insulation. Some of it will probably have to come out anyway to facilitate the new ductwork installation; the rest is often a favorite habitat for mice. Make sure to air-seal the penetrations where duct boots go up through the floor, and seal the new ductwork so that you don’t have crawl space air being pulled up into the house. Installing the rigid foam insulation against the joists in the crawl space shouldn’t create a moisture problem. Good luck.
Hi Tim,
I have a unique situation with the design of of my crawlspace. My house is also built on cinder block piers. The perimeter of the house has lattice work around the entire house, for example I have concrete pier then a 60″ X 30″ framed lattice work then another pier then another 60″ x 30″ framed lattice panel and so on around the entire house. Now one company told me that in order to encapsulate I would need to brick in the lattice frames, another company told me that I would be able to encapsulate without bricking in the lattice openings. The same company also said that I could get by with simply installing a 12 mil. barrier and replacing the fiberglass insulation. I don’t know which way to go with this. Please help me make a decision. Thank you.
Hi Janis,
It’s understandable to be confused about your options with this type of open foundation. When a crawl space has solid walls, it’s not that difficult to change the pressure and thermal boundaries from the floor to the crawl space walls. But with cinder block piers, you’ll have to go to the expense of constructing solid walls before encapsulation can begin. I don’t recommend this approach. Instead, start by removing the old fiberglass insulation and cleaning any remaining debris from between the joists. The next step is to air-seal the floor using one-part spray foam. Wherever ducts, electrical wires and plumbing lines extend up through the floor there will be openings cut in framing and sheathing. Make sure to seal these openings completely. Air-seal any ductwork that is accessible from underneath the house, although I suspect that your HVAC system is located upstairs in the living area. If this hasn’t been done already, it may be necessary to construct an insulated chase for any plumbing lines that extend from below ground up into your living space. At this stage, you can install new unfaced fiberglass insulation between floor joists, then install 1.5-in. or 2-in.-thick rigid foam insulation up against the bottom edges of your floor joists (I recommend foil-faced polyiso foam board, which is more expensive but has higher R-value and a radiant barrier). Make sure to seal all seams between foam boards with compatible tape to maintain the air barrier.
This strategy will cost much less than retrofitting solid walls beneath your house, and it will result in major comfort and energy improvements. Good luck.
I have a ranch with half finished basement and half crawl space. The crawl space is not vented to outside but actually opens to the inside – to the finished basement. My heating pipes run through the crawl space. Is it better to insulate the crawl space and leave the pipes uninsulated? Or better to close off the crawl space completely (close opening into finished basement) and insulate the pipes? There is no moisture at all as is now but since there’s no insulation, it obviously is losing a lot of heat.
PROBLEM: Crawl space opens into basement.
SOLUTION: In most cases, the best treatment will be to fully encapsulate the crawl space. Do not attempt to simply insulate crawl space plumbing and the crawl space ceiling. Make sure that air-sealing the rim joist and insulating the rim joist and crawl space walls are included in the encapsulation process. Once this has been done, you can isolate the crawl space from the basement by installing an insulated door over each opening that connects the basement to the crawl space. 3/4-in. rigid foam sandwiched between two “skins” of 1/4-in. or 1/2-in. plywood will make a good door. Adhesive-backed foam weatherstripping will create a good air seal between the crawl space door and the door frame. If you screw the door in place, you’ll be able to remove it if access is needed in the future.
The basement also needs insulation and air-sealing treatment, but that’s a topic for future discussion. Good luck.
Thanks so much for the advice. So from what youre saying, if the crawl space is encapuslated by insulating the walls and rim joint, I dont need to insulate the plumbing that runs through it?
Hi Tim —
I just bought an 1890s farmhouse that’s had a few additions over the years. Under the main part of the house is a basement with about 5 1/2 ft ceilings with cemented stone walls and small windows (4 around the perimeter). There’s no cement floor, just a skim of very thin concrete. There’s a small sump pump, but I don’t think there is any perimeter drainage. The floor (basement ceiling) is completely uninsulated as are the walls and windows of the basement. In addition, there are two crawl spaces (unvented) under two additions that adjoin the basement without any door/window or other seal (i.e. the crawl spaces open up to the basements directly). I’m trying to figure out the best solution for this basement and whether or not I can do it myself. If I encapsulate the crawl spaces, what do I do about the fact that they open up directly to the uninsulated basement? What should I do about the basement? Put in a perimeter drainage system and sump pump and then insulate the windows? What about insulating the floor (basement ceiling) and walls? Help!
Congratulations on the historic house purchase. Old houses are lucky when they get caring owners. See my replies to other comments regarding recommendations for treating crawl spaces that open into basements. Regarding your basement with a low ceiling, stone foundation walls, a sump pump and skim-coat floor: These are challenging conditions. I’m going to assume that you won’t be using this as living space. The first thing to do is to have an experienced stone mason evaluate the stone foundation walls and make repointing and mortar replacement as necessary to ensure soundness. Second task: install an interior French drain system and connect it to a new high-quality sump pump. Third, I suggest you consider either replacing old basement windows or simply cover them with insulated, airtight covers. By your description I’m going to guess that the window openings are small and your basement won’t need natural light if it’s not going to be used frequently. Finally, air-seal and insulate the rim joist. At this stage, you might just see how the house performs for a year. If too much cold is coming up through the basement, you can insulate the stone walls by applying 2-3 in. of 2-part, closed-cell spray foam. Make sure the spray foam treatment doesn’t impede drainage into your French drain system.
Tim, thanks for the great information. I have a unique situation in that I have a home with radiant floor heat via pex tubing and aluminum fins running through the joists about an inch from the subfloor. There is a thin layer of foil reflecting insulation under that followed by R-30 unfaced and string tied to complete the insulation. I am wondering about securing rigid foam to the joists encapsulate the joist bays and help focus the heat upwards. Is there a downside to such actions?
Chris
Chris: I don’t see a downside. In fact, if you tape the seams of the rigid foam sheets, you’ll create an air barrier that will help prevent convective heat loss that occurs when air moves through the batt insulation. I would just take care to make your rigid insulation installation reversible by attaching the foam with screws driven through oversize washers. If you can’t source washers, it’s possible to make your own from 2-in. squares of 1/4-in. (or thinner) plywood. With this type of installation, you’ll be able to remove a section of rigid foam without destroying the foam or making a huge mess. Good luck.
Thanks for the article. Saved me from making the fiberglass in the floor mistake. Two Questions. My crawlspace has a cement floor with about 3-4 inch space to the wall, around the entire perimeter used as a french drain to sump pump. The walls have poorly applied 1/2 inch rigid Styrofoam, attached to the concrete with fasteners. Q1. Should I attached new rigid polystyrene board over the existing Styrofoam or remove all the existing? Q2. To properly encapsulate the crawl space do I cover the cement floor with plastic attached to the rigid board, and if I do, should I run perforated pipe in the french drain space before attaching the floor covering to the wall polystyrene?
The 1-in.-thick Styrofoam isn’t providing much R-value. If it’s not in good shape, you’re probably better off replacing it with 2-in.-thick extruded polystyrene. The major benefits of covering the concrete floor with a vapor barrier would be lowering the concentration of radon that comes up through the soil (Have you had your house tested for radon? It’s a good idea to do so, especially if you have children in the house.) and lowering humidity in the crawl space. Yes, I’d recommend putting perforated pipe in the perimeter drain system before coverage with the plastic sheet.
Is there anything to be gained by placing rigid foam on the dirt floor then sealing poly vapor barrier over it?
If you live in a colder climate where the ground freezes during winter months, installing rigid foam insulation over a dirt crawl space floor is a smart idea. The floor insulation will help to keep more heat within your home’s building envelope. If the crawl space’s dirt floor is often damp, it’s smart to lay down a layer of drainage matting beneath the rigid foam. This stippled plastic sheet material is available from most Basement Systems contractors. Perimeter French drains and a sump pump are recommended if the crawl space frequently has standing water.
That poster sounded like they are leaving the vents. Insulating the floor is a bad idea in that warmth from the earth is needed to keep pipes from freezing. Even with vents closed in winter radiating cold can creep in and freeze pipes if the earth is insulated. Vapor barrier should be the only thing used.
Hello Tim,
I recently found your write up and have learned more about my CS. I put down a 6 mill barrier in my dirt floor CS 4-5 years ago but did not foam board the walls. Now I know I should do the walls and will, but I’m a little confused about the ceiling and insulating it.
Right now the ceiling has nasty decades old pink batt insulation that I did not know to remove when I sealed the dirt ground and walls. The batt was put there when the addition was built, again, decades ago. Now I know to take all that batt out ASAP, but do I put foam board in its place, between the joists, or just leave the ceiling bare?
My new plan is to remove the ceiling batt, foam board the walls, seal off and spray foam the rim joist, and re-install my 6 mill plastic barrier on the floor and walls. But what about the ceiling?
Thanks a lot!
Todd
You’re on the right track, Todd. Once you’ve removed the fiberglass batt insulation from between crawl space ceiling joists, just leave the ceiling as it is. Isulate the crawl space walls with rigid foam. Insulate and air-seal the rim joist. These two treatments bring the crawl space within your home’s building envelope, making crawl space ceiling insulation redundant. You didn’t mention sealing the crawl space vents; this should also be done to complete the encapsulation process. One vent can have a removable door or cover to provide crawls space access. Good luck.
Yup, got the vents on the list too.
Thanks again!
I live in the Chicago land NW area- my house is a old 1955 cottage converted into a 2,600 home.
The crawl is vented- it’s about 22” to 34” throughout it. I live on the lake.
It does flood every year with the thaw-and high waters from WI coming down to us “Chain of Lakes”.
It’s a dirt or mainly mud space always damp-always- it has gotten 20 deg down there but only when it gets 10 or lower for several days which that seems to keep happening—I have insulated my water pipes but the heat duct are un insulated and only cold air seems to come out when the heat kicks on—I understand the reason is nothing is insulated under the house-
I can’t use the plastic vapor barrio due to the water just pours in from the ground and above the ground – it just comes in everywhere until it recedes- I would like to insulate the concrete walls with the spray foam but don’t want to create a rotting wood effect on the wooden ceil plate- I would love to create a vapor barrier from the musty smell but don’t want to create molding or rotting wood on my floor boards—if it reached that point- last year we were 1 inch away from it overtaking the 1st floor-
What would you suggest for insulating walls or some kind of insulation with no rotting wood effect?
And some type of vapor barrier? But keep in mind it will flood.
I’m trying not to spend $12,000.
You’ve got very challenging conditions to deal with. I would suggest contacting a Basement Systems contractor in your area (go to BasementSystems.com to locate the closest contractor) as a first step. This specialist will be able to tell you whether or not it’s possible to waterproof your crawl space by installing French drains and a sump pump. This should be your first option because it will keep the crawl space area dry. Add a heavy-duty dehumidifier and you’ll seriously dry out the space, creating conditions that are hostile to mold growth. If you find that “Plan A” isn’t feasible, Plan B would be to insulate the crawl space ceiling with rigid foam insulation as described elsewhere in these comments. In this case you would keep the crawl space vented and even try to increase drainage through the space to provide an escape route for water that gets into the crawl space. This strategy is often used in seaside homes that experience flooding from storms and high tides. Good luck.
Tim,
having quite a bit of experience with crawl spaces now, I would also like to add that Kris should consider wrapping his heat ducts with insulation (fiberglass) and then encapsulating this by overwrapping them in foil bubble insulation (4′ x 125′) and sealing those seams with a high quality foil tape (not duct or duck tape as it will break down in a couple of years). This is a little pricey, but somewhat doable for the do-it-yourselfer, effective, and looks great as an end product. This will get him back to having hot air rather than cool/warmish air trying to heat his home.
Chris
Good advice, Chris. Leaky ducts can diminish HVAC efficiency by 20%. If the crawl space walls and rim joist are insulated, insulating the ductwork in the crawl space is less important than sealing duct leaks. Aluminum tape made (and approved) for duct sealing is the material to use, as you suggest.
I have a ranch style house built in 1990 and it has a crawlspace with vents. I am encapsulating it with a 12mil vapor barrier, closing off the vents, and want to install the 2″ polystyrene rigid board. The house is brick and around the exterior walls (brick) there are block support piers about every 8 foot, so they stick out either 6″ or 8″ from the brick. How is the best way to fasten the foam board, as well as seal the rim joist. Also should the vapor barrier go on the inside of foam board against brick or on the outside of foam board?
The vapor barrier can be installed over the foam board. As for installing the foam board against the foundation walls, many installers find that a combination of masonry fasteners (like Tapcon or barbed plastic fasteners) and panel adhesive is the best solution. The fasteners are mainly to hold the panels in place until the adhesive cures. Make sure that the panel adhesive is compatible with the foam board. Yes, you’ll need to cover the block supports with rigid foam to get the full benefit of perimeter insulation. About sealing & insulating the rim joist: Do this task first, when the rim joist area is most accessible.
What product do you recommend for sealing at rim joist?
Tim,
I have a tall crawlspace (4′ to 7′) with a good foil faced asphalt roofing membrane as a vapor barrier on the dirt. I already have r19 unfaced batts against the floor. It is 8 years old, in good shape, with no signs of moisture issues. What do you think about leaving the floor insulation and then sealing the brick crawlspace walls with rigid. My pipes never freeze. They are insulated and the south Arkansas climate isn’t that cold. I would hate to remove the batted insulation if it isn’t necessary. I am just trying to reduce my heating bills. I have electric heat pumps, and my winter heat cost me significantly more than summer cooling.
Thanks,
Chris,
Arkadelphia, AR
Hi Chris,
It should be fine to leave the batts in place, especially if they are dry, fully fluffed and in good condition. Definitely air-seal the crawl space walls, paying special attention to the rim joist. Insulating the crawl space walls will help reduce your heating bill, but in your case the air sealing may be even more important. Read the blogs on stack effect; this will explain how negative pressure created by escaping heated air upstairs tends to suck outside air into a crawl space or basement. Fiberglass batts won’t stop air movement, so any cold air that gets into your crawl space has a good chance of moving upstairs. If you air-seal the crawl space and air-seal the attic/living space pressure boundary, you can short-circuit the stack effect and score good savings during heating season. Good luck.
Hi Tim,
I’ve been reading everyone’s posts and find them similar to mine, but I didnt notice any of them mentioning dehumidifiers or sir systems. I have a 12 X 10 vented crawl space with a concrete floor; bought the house last year and noticed that the ceiling has batt insulation, which as you guessed it is/ was hanging down. There are two vents and an access panel to the outside, which consists of two 1/2″ sheets of plywood on rusty hinges as you can imagine. The area opens to the basement via the rim joist on one side, which I currently have insulation jammed into. The space in the summer has a lot of moisture and I’m looking to insulate and seal to keep the above kitchen floors warm and protect against mold.
I had a company come in to get an estimate on encapsulating, which consisted of the following:
1. Vapor barrier to the floor and walls.
2. rigid foam board on floor, walls, and in rim joists
3. dehumidifier
4. covers for vents
5. Sealed access panels.
Now for my questions, are all these necessary? Is the dehumidifier a necessity when the rim joists on the back side of the space open to the basement for air passage? Thanks in advance for your time in addressing my questions.
Mark
Mark: The ingredients in your encapsulation proposal sound good, but there could be some confusion about the dehumidifier. When CS encapsulation is done correctly, a dehumidifier probably will only be needed on a short-term basis –to dry out a space that has been absorbing moisture for years. Once you lower the humidity level, the moisture barriers and vent covers should keep the humidity low. However, if your crawl space is open on one side to the basement, it’s going to take longer for the CS dehumidification to take place. Assuming that the company you’re dealing with is experienced in CS encapsulation, I’d query them on a)where the dehumidifier will be installed, and b)why they wish to maintain the connection between CS & basement. An associated issue: how you will you empty the dehumidifier if it’s installed in the crawl space? Some CS dehumidifiers can be installed in a basement area and ducted to an adjacent crawl space. Resolve these issues and you’ll be on your way. Good luck.
Thanks Tim for the prompt response!
If they seal the rim joists leading into the basement thereby creating a total encapsulation of the area, is it my understanding that the dehumidifier will be used on a short term basis to initially dry the area and then seal it? With proper monitoring, over time, I would need to watch the humidity in the CS and add or remove a dehumidifier?
Thanks again,
Mark
Hi Tim,
I had another company give me an estimate on the same Cleanspace encapsulation, but this company included as an optional upgrade 4″ rigid foam board for the CS walls instead of the 2″. Is this upgrade worth it or a waste of money and I should stay with the 2″.
Thanks again,
Mark
2-in.-thick or 4-in.-thick rigid foam insulation for crawl space walls: I’d opt for the thicker insulation if I were planning to stay in the house for more than two years. The severely cold temperatures we’ve experienced this winter reinforce the value of additional insulation. I think this falls into the category of “do it once, do it right, so you don’t have to do it again.”
Thanks again Tim!
Tim, Thanks for sharing your knowledge with everyone and keeping this topic open for late comers…My house is in Northern Michigan, built on a crawl (40′ x 100′). The crawl is presently vented and the house is heated by electric baseboard. Since the crawl has no heat runs the only heat source is from hot water plumbing pipes (I will insulate them to reduce heat loss), so I’m thinking that the soil temp in the winter is 45 degrees which should basically be the same in the crawl since it has no heat runs. How do I protect the conditioned space (floors) which have R-19 insulation (apparently the recommendation for floor over unheated spaces is R-30) (house is 40 years old and I have lived there 22 of those years). One of the issues I have is the access point which is just beg enough for a person to enter through an access under the washing machine (yes, we do not go in the crawl at all). Thus, getting materials into the crawl will be an issue. Also, is there anyone pipe insulation material that is better to use over another? Thanks again! Craig
OK, so what we have here (I think) is a large vented crawl space with a difficult entry point, in an area where winters can get very cold. One option worth considering is having a spray foam contractor insulate your crawl space walls with SPF (spray polyurethane foam). If the contractor can get the two hoses through the access opening and into the crawl space, he’ll be able to coat the interior crawl space walls with 2-3 in. of SPF, while also sealing the rim joist. This will be a lot faster than moving small pieces of rigid foam insulation through the access door and then piecing them together against the crawl space walls. SPF is more expensive, but it’s very effective insulation (R-6 or more per in.) that also acts as an air and moisture barrier. A once-and-done expense. Good luck.
Tim, I have a weird situation—partial basement with crawl space adjoining it. They put in two small window like structures with screens to give air to the crawl space,I guess. Today a basement repair company said that I needed to put the plastic on the sides of the crawl space and then to seal it off from the basement. He would make a panel that could be removed if someone needed to get to the crawl space. He wants to install an EZ breathe drainage system around the basement inside and seal the sump pump. I can’t afford anything else at this time such as sumps in the crawl space. It was inspected a couple of years ago and he said it was dry. But the contractor seems to think that it’s unsafe and unhealthy to have this nasty crawl space open to the basement. Does what he says make sense? I am clueless as to the options. My basement is damp according to him because it has water spots on some of the walls. He is going to seal the obvious leaks which resulted from roofing and draining which will also be fixed later. It just makes no sense to me to have the crawl space sealed off and yet it makes no sense to me to have all that nasty vapors floating into the basement area and eventually upstairs. I would appreciate thoughts.
Becky: You’re facing a difficult situation that often occurs when an older home with a basement foundation gets a crawl space addition. Let me say up front that there’s not an easy fix for your problem. The crawl space should be encapsulated (sealed), with plastic barriers on floor and walls. I’d also recommend insulating crawl space walls with rigid foam, as discussed elsewhere on this site. When the crawl space is encapsulated, there will be no “nasty” crawl space air coming into the basement, so it won’t be necessary to seal the openings. If your basement has only dampness and water seepage (rather than standing water), I’d recommend sealing the crawl space first, then paying to have interior drains and a sump pump installed in the basement. In the meantime, do what you can outside the house to direct roof runoff and ground water away from the foundation. Good luck.
I was the one asking about the crawl space adjoining the basement. I guess what they proposed to do was the encapulation thing you were talking about. They gave me an estimate of $15000 for doing the crawl space with plastic everywhere and the ezbreathe drainage system around interior of basement. He was also going to put a proper sealed top on my sump. Thanks again.
I have a house in Alabama built in the 1880’s. The crawlspace is vented, and fiberglass batting was installed between the floor joists a few years ago. Recently we noticed problems with mold growth in one of the front rooms. I don’t have much money to spend, so I won’t be able to install spay or rigid foam underneath. What would you suggest? Based on what I read here, I would assume that it would be best to remove the fiberglass batting, put a moisture barrier plastic on the ground, and seal the outside vents. Would you agree?
I think the first step would be to complete a thorough assessment of your crawl space to see if there’s serious moisture damage (mold, wood rot) on any framing or sheathing materials. Yes, you’ll need to remove the fiberglass insulation to make this inspection. Make repairs if necessary, and contact a mold abatement specialist if there’s widespread mold. You’ll definitely want to fully encapsulate the crawl space, with moisture barriers on the floor and walls, well sealed to each other. Seal the rim joist and any wall penetrations as well. Vents can get airtight (weatherstripped) covers; same goes for the crawl space access door, if there is one. Once the space is isolated, my guess is that you will need to run a dehumidifier in order to dry out wood that has accumulated a lot of moisture over the years. Lowering the humidity of the space (and drying out the wood) is the only way to avoid additional mold problems.
A dehumidifier has been installed in the room where mold was found, and it seems to have taken care of that problem. Should all of the fiberglass insulation be removed permanently? If so, can we expect our heating & cooling bills to jump?
Removing fiberglass insulation installed between crawl space ceiling joists. We’ve had a couple of questions about this so I’ll try to clear up some confusion. If the fiberglass insulation is in good condition (not compressed, wet or inhabited by mice), it’s usually OK to leave it in place. But because fiberglass only attains its advertised R-value when installed in an enclosed, airtight space, it’s critical to air-seal the crawl space. Pay attention to vents, crawl space access doors and the rim joist. Consider replacing old, single-pane crawl space windows with vinyl, insulated glass windows. Complete the encapsulation process with moisture barriers on floor & walls. If the crawl space was damp for a long time before encapsulation began, dry out the space with a dehumidifier to create a mold-hostile environment.
I’m very much in the same boat as Kathy from Savannah. Same town and same open pier crawlspace. I would like to add crawlspace walls to the perimeter. I need to do this for critter control. They are tearing up my flex ducts. Long term, I would like to encapsulate. Would it be better to go with hollow concrete block or frame it out with hardi-board panels. Either way, I was planning on pouring footers. Do I need to vent the walls? So far everyone is telling me I should. As of now, ground vapor barrier only only covers 90% and the joists are mostly clear of batt insulation. Previous owner tried to install unsuccessfully in several locations.
If it were my house, I’d skip the block walls because I don’t like the appearance and because I’m a carpenter. So I’d use p-t lumber to frame crawl space walls, and finish with Hardiboard panels as you suggest. I’d frame & finish an access door with beefy stop molding that would accept equally beefy weatherstripping for maintaining a good airseal. No vents. Assuming there’s no groundwater problem (soil stays dry), install a good plastic moisture barrier over the ground. I’d probably opt for mineral wool (Roxul) insulation between joists in the crawl space walls, then fasten 1-in.-thick foil-faced rigid foam insulation against the inside edges of the studs, taping the seams to seal air leaks. It would be smart to make provisions for running a dehumidifier in the crawl space even after it’s sealed. Wood stores a lot of moisture, and it will need a way to dry out after the crawl space is sealed. This treatment will take more time, trouble and money than treating your first floor framing as the thermal & pressure boundary, but it will eliminate the pest problem, help your HVAC performance, and put a better-looking foundation on your house. Good luck.
Hi Tim, question for ya. I have a three level split with crawl space under middle level (in mn). i am going to insulate the wall and rim joists and lay down new vapor barrier like you’ve suggested. the crawl space has an HVAC vent in it so it is heated in winter and cooled in summer. there is a regular interior door that accesses a closet that is open to the crawl space. after I encapsulate the crawl space, will it still be ok to have just an interior door closing off the crawl space from the downstaris? how do I run the vapor barrier against the downstairs wall (studded and no insulation?) Also, i would really like to use it for storage since its conditioned, but i dont want to ruin a new vapor barrier. Could i throw down some 4×4’s and screw decking boards to them force platform for staorage? will that be ok to sit on top of the poly. thanks
Once the crawl space is encapsulated, it will be within your home’s building envelope, so the interior door should still be fine. Don’t attempt to run a plastic vapor barrier up along a bare studded wall. Instead, install foil-faced rigid foam insulation against the stud wall, and tape all insulation seams with aluminum tape. The foil facing will act as a vapor barrier as long as it’s continuous; use sealant to adhere the plastic vapor barrier to the foil facing. It’s fine to use the crawl space floor for storage, but (as you point out) care must be taken not to tear or perforate the floor vapor barrier. One strategy would be to build wood-frame platforms as you suggest, but glue some rigid foam insulation to the underside of the framed platforms so that sharp wood edges don’t tear the plastic. It’s also smart to remove sharp rocks from a dirt crawl space floor before laying down the vapor barrier.
Good luck.
Thanks for the info. I like your suggestions and will be doing just that. Thanks again, i really appreciate it.
Hi Tim,
I have a small frame 2 story in Chicago area built in 1938 with a small crawl space addition. The CS is not vented and the access door is outside. The space seems dry and framing in good shape but the batt insulation is falling down and dirty. This house is different in that it has a concrete foundation but only up to 3 in. above grade, and then it’s wood studs and sheathing on up. The joists are nailed to the sides of the studs 3 ft. above the top of foundation, and there is a ledger board underneath supporting the joists. There is no rim joist. Outside crawl space walls are also framed with plywood sheathing on top of a short concrete foundation. Question is how do I properly insulate the wood walls of this CS? Also, should I open up this crawl space to the heated basement or should I just keep it sealed off from it? House is heated with hot water and there are no pipes or ducts in the CS.
The framing detail you describe tells me that your house has “balloon framing,” a framing technique that was used extensively around the country until “platform framing” began to take over in the 1960s. It’s good that your crawl space is dry, but it should still be air-sealed and insulated, especially given your climate. Remove the old, dirty fiberglass insulation. You could have a spray foam contractor spray closed-cell foam between the joists, behind the ledger, and along the top of the foundation. Alternatively, you could friction-fit rigid foam insulation between the joists and fill gaps with one-part foam (GREAT STUFF). It would be wise to insulate the crawl space walls with 2-in.-thick rigid foam insulation. But before you install any new insulation, see if you can determine whether there’s any insulation in the walls. With balloon framing, the stud bays you see in the crawl space or basement extend all the way to the attic. My guess no wall insulation, unless it was installed more recently. If the walls of your house are without insulation, I suggest reading up on blowing dense-pack cellulose or injection foam into your walls.
Thanks for the advice! I can look up into the open stud bays from the basement. There is some insulation that looks like thin 1/2 or 3/4″ paper “batts” of what looks like some kind of brown sawdust material, covered front and back with the paper. I found this in the kitchen when I gutted it and it’s just tacked to the sheathing and crumbles easily when touched. The addition is recent and is framed in the platform fashion with a rim joist which is supported by the short stud wall which rests on the concrete foundation. The walls of the addition above the floor are insulated with fiberglass. If I use the rigid foam insulation for the basement and CS stud walls, which type should I use, and I need to use a vapor barrier over it? tAlso should I have this CS open to the basement using vents or a louvered door or should it be sealed off from the heated basement?
Hi there,
I recently bought a beach house in northwest Washington state. Built in 1966, and seems to be in fine condition. Went into the crawlspace on the weekend to check things out. Very low 18-24 inches below the joists. Dry dirt floor. No mold, thankfully no batts of gross insulation, but plenty of beer cans and gin bottles from the 1960’s! I cleaned out all the crap and sharp rocks and I am ready to encapsulate the 500 sq/ft space. The floor is undulating, but think I can make do. I have a few questions:
1. The entry door is on the exterior wall, through the foundation. Rim joist on top. Dirt bottom with the septic pipes exiting through the same space. How can I frame in the doorway so I don’t damage the pipes that are just below the surface? (Form and add concrete? Brick bottom and frame P/T above?
2. Foundation walls are 3 feet or less. I was going to encapsulate the floor, up the walls and around posts. Can I add rigid foam insulation after I and vapour barrier?
3. Crawlspace door is below grade with a slope down towards the entry way. Should I buy a galvanized entry tub and Lid to eliminate possible flooding?
4. What are your thoughts about DIY spray foam for the rim joist bays?
Thanks for your help and awesome info site!
Gregory:
Thanks to sandy soil that drains well, beach houses often have excellent drainage and few moisture problems. This appears to be the case with your newly acquired house. Let’s see if I can help with your questions.
1. The entry door. Don’t encase the plumbing pipes below the entry door in concrete; this will make it impossible to repair/replace these at some future date. Instead, dig around the pipes below the entry door, encase the pipes in tightly packed sand, and then lay down a layer of brick to form the bottom of the doorway. I recommend joining the bricks together with construction adhesive rather than traditional mortar. On top of the brick, you can bed a pressure-treated 2x sill in construction adhesive; this will form the bottom of your door frame, which will require a weatherstripped, airtight door that can simply be screwed in place on the 2x frame.
2. Insulation. If you’ve got fiberglass batt insulation between CS joists that’s dry and in good fluffed condition, I’d simply beef up and air-seal this thermal boundary by fastening foil-faced foam board to the underside of CS joists. Tape the seams and edges to air-seal this insulation layer.
3. Not sure about what is meant by galvanized entry tub. If there’s a recess in the ground where you fear water will collect against the CS door, then this is probably worth covering with some sort of light frame topped by corrugated plastic roofing material.
5. Definitely insulate and air-seal the rim joist. It will be less expensive to precut rigid foam inserts to friction-fit between joists and against the rim joist, then seal around their edges with one-part spray foam. Obviously you’d want to do this before installing the rigid foam insulation as explained in #2 above. Good luck.
Hi Tim,
Enjoyed reading all the posts, and of course have a different situation that wasn’t answered 🙂
I have an old church built in 1874 that has concrete foundation. Its built on top of a hill, where the bedrock was bare. Hence, a very uneven floor under there. There is natural runoff, so I put french drains throughout and then poured cement to cover all the aggregate. This will hopefully prevent any standing water. The crawlspace will be sealed to prevent condensation.
I’ve been toying with the idea of putting a couple of baseboard heaters down there. It would be nice to have warm floors. Its in Newfoundland, and the spring and fall are sometimes colder than winter. May 6, and we got nearly a foot of snow today.
My questions are:
Should I put a vapor barrier over the cement/bedrock?
What are the pros/cons of heaters? It doesn’t seem like anyone else does them.
Is it possible to insulate the concrete/bedrock itself? If it was level, I would be able to lay foam sheets, but that won’t work in this case.
There is no access to the foil/shiny type of insulation that seems to be what most people are using. Is there any reason not to use the 2″ blue or pink sheets? Might even double them up to get the extra r value if they are ok.
Thanks!
Gary
Hi Gary,
Don’t put baseboard heaters in the crawl space. Heat moves from more to less, and the “less” in this case will be the bedrock floor and concrete walls of the crawl space. If you plan to turn the church into a residence, I suggest testing for radon. This radioactive gas emanates naturally from rock, which you have in abundance. Installing a thick poly vapor barrier over the floor and up the walls should go a long way toward reducing radon levels, but have the test done anyway.
The rim joist area is sure to be very leaky, so seal and insulate this perimeter zone as described elsewhere in these comments. Install 2 in. of rigid foam insulation against the crawl space walls, and keep this thermal boundary effective by installing insulated, weatherstripped covers for crawl space vents and the crawl space access door. Once you’ve made these improvements, you may not need insulation on the crawl space floor. If you still feel too much cold coming up through the floor, Basement Systems has a product called TerraBlock(r) that is flexible enough to flex over an irregular floor surface. Good luck.
Thanks Tim, really appreciate that you are sharing your knowledge here. This issue seems to be a hot topic.
Hi Tim,
We have a Ranch style house in a Beach town on Long Island. Hurricane Sandy flooded our 2 ft crawlspace. After the storm, we had the insulation removed by a contractor and he re-insulated the crawlspace with fiberglass batts (that were installed with the vapor barrier down) and then attached 1′ Tuff R foam board to the joist, but it was not taped and sealed as you had mentioned. Unfortunately, a recent inspection revealed that there was mold growing on the joist that were insulated by this method. We don’t know if the mold was just not removed properly or it grew from the method he used.It doesn’t matter, we just want to do it properly this time.We had all the insulation removed and saved the foam board as it looked fine and now its time to re-insulate. The mold has been re-mediated by a professional and re-inspected to satisfaction. We have a proposal to encapsulate as you have described. It will re-use all the Tuff R on the walls (after disinfecting them for safety). We have enough to use 3 layers, providing R-18 or so. The floor, which is sand, will be covered with a 6mil plastic and taped to the walls and center supports. The rim joist and open foundation block cavities will be sealed with 2 part spray foam. The whole area will be fogged with an anti-microbial solution. Crawl will be air tight. My questions are;
1) Does this sound like a good proposal?
2) Is it okay to leave the areas between the joist uninsulated? I noticed in some of the pics above that they have both the walls and the joist insulated.
3) Should we run a self pumping dehumidifier down there or is it unnecessary?
4) Do you think its better to just insulate the joist again and seal it with the foam board in our situation?( meaning we are in a beach town) The crawl seems to stay relatively dry unless its a major storm, but we are afraid it it takes on a little water all will be ruined with the encapsulation method.
sorry for the long post, but I wanted to be clear. Thanks in advance for you help!
Hi Scott,
Your proposal sounds good. It’s OK to leave the spaces between the joists uninsulated. Now for the important part. Given the level of wetness your floor framing was subjected to, and the fact that you had serious mold, I’m quite sure that you still need to dry out the wood in your crawl space. Don’t reinstall the Tuff R until your framing and floor sheathing are dry, because doing so will trap moisture that will attract new mold. So yes, I would run a dehumidifier in your crawl space until you get below 50% humidity, if possible. Make sure to cover crawl space vents with airtight covers so that you isolate crawl space air. In a flood zone, conventional encapsulation is not usually recommended because a storm surge exerts too much pressure against the foundation. Instead, many homeowners have flood vents installed, and put rigid insulation on the underside of the floor joists, as you’re doing. The flood vents stay closed under normal conditions, but will open automatically if the water level rises to the vents during a storm. By allowing flood water to flow through the foundation instead of driving against it, there’s less chance of severe destruction. Flood vents can mean lower flood insurance too, so they’re worth checking out. Good luck.
Great posts here – I do have a little bit of a different situation… I have a house mad of cement and cinder blocks. The outside walls (and some inside walls) are cinder block up to the roof. We have cement floors and ceilings and Cement support beams holding the floor up. This winter was very very cold and the basement was fridgid. My question is can I simply insulate the walls with 2 inch foam board all around the outside walls and not do the Cement Ceiling? or should I just do spray foam on the cement ceiling and not do the walls? or do i have to do both? Spray Foam is very expensive in NY and the installer is telling me I have to do 3 inches to have a vapor barrier (is this true?).
Fernando: The house construction you’re describing is very unconventional –masonry walls and even concrete floors. You may not like my answer because it’s an expensive one, but given your situation, it’s what I’d recommend. Your exterior walls need to be covered with rigid foam insulation –at least 2 in. of polyisocyanurate foam board (foil-faced polyiso board). This work needs to be done by an experienced carpenter because it’s not easy to fasten the foam to the masonry, and then fasten wood nailers to the foam so that exterior siding can be installed. Window and door openings will need extension jambs to bridge this added wall thickness. To properly insulate the building exterior, you’ll need to extend the foam board 2 ft. or so below grade. Like I said, you’re looking at a lot of work here.
Thank you for that info! I am planning on doing the foam board on the outside of the house where we can (as the front has stone already). Have you heard of the insofast product? What do you think of it if you have? Thank you again!
Hi there- I was just reading through your posts and enjoyed them. I am a first time home owner. I live in Cinnaminson, NJ – I live in a 20 year old home and it has a pretty deep crawl space. approx 5′ deep. It has a concrete floor and one sump pit – improperly dug only 1 foot deep with no bottom and a second crock installed with no sump. Before I moved in there was a little water – and the homeowner had a wall drain placed in with a lead to the sump. Two months into living there- I have had nothing but water problems in the crawlspace. I have had 4 contractors come out quoting me anywhere from 9,000 to 19,000 to fix. I have had someone from basementsystems come out – and he said that with a cement floor – it can be treated like a basement and not a crawlspace. I have had another contractor say that it needs to be fully encapsulated. The basement guy stated that he would dig a trench but not re-cover with cement? – Another person stated that all I needed was a perimeter drain. I have also heard some say seal off the vents – others say no need to seal off vents. All of them have said that I need a dehumidifer permanently running in the space. How does one know what is right? – I also watched a sight stating that using PVC pipe or those metal drains that basement systems use don’t work and you should use ADS tubing? – So hard to determine – all I want is to make my life easier by not having to worry so much – been battling water for 4 months now.
Sorry to hear about the water problem and the confusion. If you truly want to stop worrying about water in the crawl space, I suggest going with the Basement Systems dealer. I haven’t seen a better system for keeping basements and crawl spaces dry than theirs. Address your water issues first, then address the encapsulation. If you have storm-related power outages in your area, I suggest installing a sump pump (like the TripleSafe model from Basement Systems) that includes battery backup, to ensure that your system will keep working when there’s a power outage. You can get cheaper waterproofing done –like the open trench approach you described. But when it comes time to sell your house, the WaterGuard concealed perimeter drains and nice-looking sump pump system will impress prospective buyers instead of scare them like open trenches will.
Thanks Tim,
I do have one more question – do you encapsulate a crawlspace with a concrete floor? – I have seen conflicting things on this. Also – one website I saw had videos of a guy ripping out the waterguard system. The waterguard system – is placed at the footer as opposed to below the footer. The video showed that the water was below the footer and questioned how water was supposed to get into the waterguard?
A French drain that’s installed below the footing will definitely capture groundwater at a lower point that the WaterGuard system will. There are several problems with this lower drain position, however:
1. It’s more expensive to install, since much more concrete and soil will need to be dug up.
2. Any drain located in the “mud zone,” at this lower level, will be more prone to clogging with silt over time.
3. It’s not possible to clean out this type of lower drain.
4. Lower drains won’t capture water that seeps through foundation walls.
One of the best things about the WaterGuard drain system is that you can install inspection ports that allow you to inspect and clean out the drain. As long as your concrete slab isn’t riddled with cracks that admit water, hydrostatic pressure is going to force water up along the wall-floor joint, which is where the WaterGuard drains are located. Don’t get me wrong –no waterproofing system is perfect. But I think the WaterGuard system has more advantages than other systems.
Dear Tim,
We just bought an 1820s farmhouse in Massachusetts with (i) a basement with a partial cement and partial dirt floor, and (ii) two dirt floor crawlspaces. The basement will always be wet — there’s a portion of it that sits just above the water table. A boiler, hot water heater, and oil tank are in the basement. The crawl spaces are better off, because they’re higher and therefore don’t get the water from below. There’s a furnace in one of the crawl spaces.
We don’t want to reclaim the basement for living space, but do want to keep it and the crawlspaces as dry and mold-free as possible, and we want to prevent mold and other bad stuff from coming into the house through the chimney effect. (The basement and the crawl spaces are connected via a porthole-like vent.)
What has been proposed to us is closed-cell insulation in the floot joists above both the basement and the crawlspaces. We’re told it’ll do the trick by keeping moisture below, which we’ll reduce/eliminate by installing a sump pump and dehumidifier in the basement.
However, what I’ve read here and elsewhere is that we should vapor barrier the floor, closed-cell the walls, and leave the joists untouched, essentially making the crawl spaces and basement conditioned space.
What do you think? Will our plan (which seems to be required by the building code) work, or are there downsides to it? Is some sort of encapsulization with plastic sheeting necessary, even if we put closed cell above in the floor joists? Anything else I should be considering?
Thanks for any guidance you can provide.
Hi Gus,
Sounds like this old farmhouse has found a caring new owner; that’s good news. I share your concerns about moisture & mold. But don’t try to do everything at once. Above all, don’t apply closed-cell foam between the floor joists before drying out the basement, because this can actually trap moisture in your framing and make the mold invasion more severe. Waterproof & dehumidify the basement first. Get it dry, so you’re creating a mold-hostile environment. With an old farmhouse, this may also mean improving exterior conditions to drain roof runoff and surface water away from the house. Have an interior French drain and sump pump system installed in the basement, along with a dehumidifier that drains into the sump pump. I think that Basement Systems has the best interior-based waterproofing system available, including SaniDry dehumidifiers that have air filters capable of trapping mold spores. Have a heavy-duty moisture barrier installed over the basement’s dirt floor, sealed to the walls & the concrete floor.
When you complete this initial phase, the next step is to air-seal and insulate the rim joist (which may actually be a large sill plate in an old New England house). Because of the HVAC equipment and water heater in your basement and crawl space areas, it’s better to insulate your foundation walls to bring these areas inside your building envelope. This can be done with spray foam, as long as the foam application doesn’t prevent wall seepage from flowing down to your interior French drains. Stone foundation walls are good candidates for spray foam insulation, because the irregular surface makes it difficult to install rigid foam panels. Good luck, Gus.
Very interesting and informative page this is. And I sure could use some advice. 10 years ago I purchased an one bedroon Apartment turned Condo that is on the corner end of 6 attached manufactured units. One big crawl space under all. There was fiberglass insulation with plastic barrier on the underside of my flooring which now, all the plastic has rotted and the fiberglass hanging down. The crawlspace floor is fine gravel and sand or such. Four open vents, two on each side of the crawlspace. So I’ve only just learned that adding the plastic to the underside of the floor is bad for trapping moisture with the fiberglass. I won’t be able to line the entire crawlspace. I won’t be able to seek assistance from the Association. Would it help my condo by removing the old fiberglass and lining my own dirt floor with plastic? Not sure what I can do being part of 5 other units. Not sure what my best otions are for my situation. Any help appreciated.
Many condos were built just like yours. Unless you can band together with the other owners, I don’t see how you could isolate your crawl space. Unfortunately, leaving the crawl space as it is will lead to problems with mold and wood rot, not to mention poor energy performance. My suggestion is to see if you can start a movement to encapsulate the entire crawl space. In the end, it’s much cheaper than replacing rotten framing material.
Thank you for responding lightening fast! and..I knew you were going to say that 🙂 When I purchased 10 years ago it was $90,000. Now worth at best $11-15. Seriously. People are renting them out with little consideration to repairs. These were built in 1986. So I guess one last question again about the fiberglass. Being on my own here, am I better off replacing the fiberglass and plastic barrier sealing it in or removing all of it and perhaps closing off my vent so water can’t get under my side? Put it back the way it was or leave it open. I’m in florida, not worried about cold floors. OY. 🙂
Hi Tim,
I hope you’re enjoying your Memorial Day weekend! My wife and I bought our first home, a front-to-back split level (built in 1955) on Long Island, NY last summer. With a new baby and everything going on with our move I didn’t pay too much attention to our crawl space until Fall. The CS has a concrete floor with a foundation vent on each side of the house. One vent was closed and the other was falling apart. It was built in to the foundation when it was originally poured. I added fiberglass insulation to the floor joists because our kitchen floor above got very cool. I also bought one of those $15 foundation vents that open when temps are above 70 degrees and close below 50 degrees. Despite below average temps, the winter wasn’t so bad. As spring arrived, I recently noticed a damp odor in my den. There’s a cut-out access door to my crawl space in the den. The more research I do, the more I’m finding that it’s better to seal both foundation vents and encapsulate my CS.
Do you recommend I do away with the vents, seal them with a wood cut out, spray Great Stuff over them and apply rigid foam board to the CS walls? If I do this, is there still a need for the fiberglass insulation in the floor joists? Do I need to put Poly sheets on the floor still even though it’s not a dirt floor?
Although the home passed a termite inspection, the previous (and original) owner disclosed they had termites in the past. There was actually a lot of old pieces of wood trim and some 2×4’s which I immediately removed from the CS.
John:
You were smart to remove the scrap wood because it attracts termites. Based on your description, I would say that you’ve got excess moisture in the crawl space, along with its most common symptom: mold. Because of the termite issue in the past, I suggest having a termite inspection done again. You definitely want to encapsulate the crawl space. This means a moisture barrier over the concrete floor, sealed to a moisture barrier on the walls, and a complete air-seal of the rim joist. Install airtight, weatherstripped covers over the crawl space vents. You’ll also need a dehumidifier running in the encapsulated crawl space to dry out the air and the moisture-saturated wood and create a dry environment that’s hostile to mold. Instead of using a dehumidifier with a reservoir that requires regular emptying, I suggest one equipped with small pump that will automatically pump your condensate to the exterior. Alternatively, you could let the pump drain into a sump pump in the crawl space. If the fiberglass insulation you installed is OK, it’s fine to leave these batts in place. See how your encapsulated crawl space performs this winter; it could be you don’t need any additional insulation.
Thanks A LOT Tim! I have already scheduled a termite inspection and plan on tackling the rest within the next two weeks.
Which moisture barrier do you recommend on the concrete floor/walls? Also, do I put the moisture barrier over or under the rigid foam boards and what size rigid foam should I get and where can I get it? Is Great Stuff Brand spray foam sufficient for the rim joists.
I have access to a dehumidifier with a 40 foot hose, which I will run once the space is inspected and encapsulated.
John on Long Island: 2-in.-thick extruded polystyrene foam board is a good choice. Or you could use polyiso board, which has a foil facing. In addition to installing the foam board against crawl space foundation walls, you can cut small rectangles of foam to friction-fit between joists along the rim joist, then foam around the edges with Great Stuff. If you seal and tape the joints between foil-faced insulation board, no plastic vapor barrier will be necessary.
The big caveat here is that if you live in a flood zone, you’ll be better off installing the foam insulation against the underside of crawl space joists.
Greetings and many thanks for a well-done job.
A bit of information, then questions.
1. 40 year-old house is in Pacific Northwest, close to ocean, on well-drained sandy soil.
2. 40′ X 20′ crawl space, concrete floor, concrete walls.
3. Screened vents 36” X 3″ at gable ends, plus 24″ X 32″ door at middle of front. Vents are uncovered April until October, then covered.
4. Floor joists are 40″ above CS floor.
5. Fiberglass between floor joists. No other insulation, vapor barrier on CS floor, walls, rim joist.
6. Stored materials – building lumber, camping gear, junk – have not corroded, rotted, mildewed, molded.
7. Some, not all, of the fiberglass is sagging, falling out.
Questions:
1. What is best fix for sagging, falling fiberglass – anything that can simply be rolled or stuffed in between joists without removing all fiberglass?
2. Have I just been lucky in terms of damp, mold, mildew, and should I seal/insulate CS walls, or is it best to leave it for another 40 years, venting as described above?
Alan:
Yes, you’ve been lucky. But you don’t want to tempt fate, so I suggest a few improvements. You didn’t mention whether or not the rim joist has been sealed and insulated. I’m assuming it hasn’t, which means that this should be done. You’ll have to move some fiberglass insulation out of the way to friction-fit rigid foam (2-in.-thick extruded or polyiso board) between joists against the rim joist, then seal gaps with spray foam. Replace the bad fiberglass with new unfaced batts. Then install a layer of rigid foam (foil-faced polyiso board, 1 to 2 in. thick) against the underside of your crawl space joists. This should significantly reduce air infiltration and heat transfer at your thermal boundary, which in this case is the floor. A full encapsulation (moving the thermal boundary to foundation walls, sealing vents & opening) would also work, but it’s more expensive. As long as your crawl space continues to stay dry, this is probably the most cost-effective strategy.
Tim,
We have a log sided great room addition that has an access door in floor to 3′ crawl space below which is not attached to basement. It has two vents that we open and close in spring and fall. This past winter it became difficult to heat the cathedral great room because of air infiltration which was coming from the crawlspace (harshest winter in years). We are adding radiant floor heating to the existing hot water baseboard heating we have currently. The heating contractor said he would remove the fiberglass insulation from the floor joists below and install the radiant heating/insulation but recommended that we have the CS walls sprayed with foam insulation. The insulation contractor concurred and said he would block off and spray the two vents, box joints and walls. Is all of this correct? The CS is dry but the old insulation looks like a cave down there.
You definitely need to insulate the crawl space walls and close off the vents. The spray foam treatment will also include sealing and insulating the rim joist, which is very important. Removing the fiberglass insulation is also a good idea. You didn’t mention whether your radiant heat tubing will be installed on top of the floor sheathing or stapled to the underside of the sheathing, running between joists in the crawl space. If it’s the latter, I’m guessing that your contractor will recommend installing a radiant barrier beneath the tubing, to help reflect heat up toward your living space. Good luck.
Tim,
I have enjoyed reading all the posts and your responses. Our house is on an island in SE NC and has a vented crawlspace (18 @ 8″x16″ vents) with a sand floor covered with plastic. The SC ceiling had 6″ fiberglass batt insulation which was sagging so I removed it all. We have two issues to deal with – flooding and termites. We have had neither to date BUT both are possible! I was planning to encapsulate the crawlspace by doing all the right things – cover and seal all vents, air seal the rim joist with spray foam, 2″ rigid foam insulate the walls and pillars, 6 mil vapor barrier on floor and up the walls – while leaving a 3″ termite inspection gap between top of wall insulation and sill plate. With the flood potential, should I just air seal the rim joist and add rigid foam under the floor joists? How much rigid foam is required in zone 3? What about the rest? Leave the vents open? Sand floor covered with plastic? Leave the block walls uninsulated? Your comments would be appreciated. THANKS
Hi Charlie & Marlin,
In a coastal flood zone, crawl space encapsulation takes a back seat to flood protection measures. Consequently, you want your thermal & pressure boundary to be the crawl space floor assembly. Insulate & air-seal the rim joist. Then use either spray foam (2-part closed-cell foam) or rigid foam to insulate between the joists to R-12 or so. Your aim is to meet or exceed the minimum recommended level of R-19 for floor insulation in your climate zone. This can be achieved with a couple of inches of foam between joists, and a continuous layer of foil-faced polyiso board secured to joist bottom edges (seal the joints with aluminum tape).
Consider installing flood vents in all your vent openings. These vents stay sealed shut until rising flood waters trigger them open, allowing flood waters to flow through the foundation rather than beating against it. Flood vents might lower your flood insurance; it’s worth investigating.
Now for the termites. These critters prefer wood that’s moist, so your best preventative measure (apart from treating the foundation) is to keep moisture levels low. Also, try to limit the amount of moist wood (such as damp piles of firewood) on your property. Good luck.
Tim,
Thanks for the quick response. I have some follow-up questions. My joists are 12″ deep wooden I-beams spaced 19″ apart; if I apply a continuous layer of rigid foam to the bottom edge of joist, do I need to insulate between foam and subfloor (what is R value of 12″ dead air space)? Can I obtain an R-19 with 2-3″ of rigid foam and 12″ air space? Also how do I control moisture if I don`t seal vents and cover floor? Any thoughts on painting concrete walls with water sealer to control moisture wicking into crawlspace. Please advise. Thanks again!
Let’s back up a bit. If there’s a moisture problem in your crawl space, your best solution will be encapsulation: moisture barrier on floor (with perimeter drains & sump pump if you regularly have standing water), rigid foam insulation on walls (2 in. extruded polystyrene), sealed vents, sealed & insulated rim joist and a dehumidifier running to dry out accumulated moisture. Once the crawl space is dry, you can stop running the dehumidifier. If your crawl space is relatively dry, moving the thermal & pressure barrier to the floor (the options discussed earlier) would be a good treatment in a coastal flood zone. If it isn’t, I’d opt for encapsulation with moisture control as mentioned.
I may have been a bit confusing when I mentioned floods and termites, they are concerns (not issues) since we`ve had neither. Moisture control is THE issue at hand. When I removed the fiberglass batts it was because they were looking like “drunken stalactites” and plastic on the floor has water droplets beaded up on top. Last week I measure the crawlspace temp at 70 F with 80 RH. My guess is you`d recommend full encapsulation as stated in earlier and leave the floor uninsulated. One last question, after full encapsulation do I need to supply any conditioned air to the crawlspace? Thanks again!
OK Charlie,
You’ve got the classic warm climate moisture problem in a crawl space. Hot, moist air enters through CS vents and condenses on cooler surfaces. Encapsulate the space, making sure to air-seal well (stop the warm, moist air from entering). An effective moisture barrier (plastic sheet material) over the soil floor is also important. Then you’re going to have to run a dehumidifier to dry out the space. Once you get the CS dry, you shouldn’t need to supply it with conditioned air. It should stay fairly dry, because you’ve isolated it from exterior & ground conditions.
Hi Tim,
I’m looking at building a home that will have a 5 foot concrete, un-vented crawl space (with concrete floor). What is my best option for insulating it? Is an insulation blanket a bad idea? We are in the North where the ground does freeze in the winter.
New construction presents insulating opportunities that aren’t easily available with retrofits. After the formwork comes off the walls of your crawl space and before backfilling begins, you can install 2 in.-thick extruded polystyrene rigid foam against the outside face of your walls. You might also want to install a dimpled drainage mat like Delta -MS from Cosella-Dorken. It’s MUCH cheaper to do this now than as a retrofit. If termites are a potential problem, make sure to extend the metal termite shield across the full width of this wall assembly. Bringing the foundation’s mass within the building envelope should help with energy performance. Also in the “while-you’re-at-it” category: installing rigid foam insulation beneath the crawl space slab floor to show heat loss in that area as well. Good luck.
Thanks, Tim! I don’t believe termites will be an issue. So you’re saying install rigid foam before the crawl space floor is even poured?
So I live in western Washington…. I need to re-do my ramblers crawl space….my plan is to remove all the pink stuff….and replace the floors vapor barrier with new plastic but I also plan on putting rigid foam on the short walls and under the floor…it that the right plan….and can you staple plastic sheeting on the ceiling side too over the rigid foam for even more moister protecting……. basically rigid foam between joists and down the walls to a 10mil vapor barrier floor.
Building scientists stress the importance of aligning the thermal, moisture and air barriers. So installing two moisture & air barriers in two different locations isn’t recommended. I think the best strategy is to stick with traditional encapsulation. Insulate & air-seal the crawl space foundation walls & rim joist. Insulate & air-seal the floor. Manage moisture in the crawl space with a waterproofing system & dehumidifier if necessary.
Thanks Tim……so the plan is…..3″ rigid foam sheeting between the floor joists…..1″ foil backed rigid foam for the foundation walls….and 6 mil plastic sheeting on the floor. But many say plug off all the vents to the crawl space and make it air tight no fresh air venting…is that really what I want to do????
The encapsulation process recommended by building scientists is supposed to isolate the crawl space interior from exterior temperature, moisture and air conditions. This is a universal recommendation except when a house is located in a flood zone, where flood waters are likely to rise to first floor level. In these locations, it’s better to insulate and air-seal the crawl space floor, and install flood vents in crawl space walls that will automatically open during floods.
Tim, Have you ever run into ANTS in a crawl space? I just found a large number of them behind a piece of rigid foam insulation that we glued against the concrete block foundation to insulate the walls. They have been finding their way up to the kitchen and are driving me crazy! We recently sprayed the entire perimeter of the house with an industrial poison after noticing a number of runs from the ground to the sill plate. I have also tried numerous times to put out borax mixed with honey and water. They seem to love it and eat it extensively for a couple of days. They then disappear for 5 or 6 days, but always return. What can we do??
Your ant problem sounds like it deserves the attention of a pest control professional. The most effective strategies to deal with pest problems usually focus on creating hostile or unattractive conditions. Applying an appropriate pesticide to the crawl space is certainly one such strategy. As for the steps you can take, keeping the crawl space dry is a good idea. You’ll also want to address what is attracting the ants upstairs –any type of food or trash that isn’t packaged or covered properly. Good luck.
Then, a specially trained and licensed remediation expert will remove the
mold infected portions of your home, or contents, and take them to a
hazardous waste dump for disposal. The cooler surfaces of a crawlspace or
basement act the same as the can. Chlorine is a powerful whitener and disinfectant, but
can cause negative health effects in people, plants, and
animals.
Great article! Would it be better to first place plastic on cement blocks before placing the foam board?
See my earlier comment about XPS & polyurethane foam board.
continued…. it appears some installers are placing the plastic on the wall before placing the foam board? Your thoughts?
Extruded polystyrene (XPS) foam and polyurethane foam board can usually provide sufficient moisture barrier protection when installed against foundation walls. So the added expense of a poly sheet barrier is not necessary.
Hi Tim,
My crawlspace has a dirt floor and is unvented. The furnace ducts and water pipes run through the crawlspace below the floor joists. I plan to insulate the cement block walls with rigid foam board. Should I also insulate the metal ductwork? Or does some heat loss from the ducts help keep the crawlspace warm? Or maybe I should cut a vent in the ductwork to have some warm air blow into the space? The water pipes are insulated and have heat tape on them.
Another question: the house is in the Rocky Mountains and the crawlspace has been bone dry for 30 years…and has never had a vapor barrier on the dirt floor. Is it still necessary to install a vapor barrier on the dirt floor?
Thank you very much!
Insulating the crawl space walls will bring your ductwork inside the building’s thermal envelope, so there’s no need to also insulate the ductwork. However, it’s important to seal the ductwork. In the winter, some heat transfer will take place in the crawl space through your ductwork system, and this should provide a measure of protection against pipes freezing. I’m glad your supply lines still have heat tape as extra protection against freezing. You mention that the crawl space isn’t vented. If there’s an exterior entry door, make sure that the door has effective weatherstripping to maintain a good air seal; the door should also be insulated with rigid foam. OK, now for the moisture barrier over the dirt floor. It’s great that your crawl space has remained dry. As soon as possible, I’d have a radon test performed. Without a moisture & air barrier, there’s no impediment to radon gas, and you don’t want to risk steady exposure to this radioactivity. If your radon tests above 4picocuries per liter, cover the dirt floor with a poly sheet that’s sealed to the walls and retest. If your radon test shows results below the mitigation level, I suggest going through the next year and seeing how your home performs. In really cold climates, rigid foam insulation is sometimes installed on the crawl space floor –but this may not be necessary in your case. Good luck.
I live in NC in a house with a vented masonry foundation and drooping insulation. There’s a gas furnace (split system) in the crawl space, so I’m concerned about fully encapsulating the C.S. Last year, I had a dehumidifier installed in the crawl space to combat high moisture. The contractor also sealed six of the eight C.S. vents, leaving two vents open to provide fresh air to the furnace. I plan to insulate the rim joists as you suggest, but I’m reluctant to remove the old insulation. Questions: 1) can I safely encapsulate the C.S.,even with the gas furnace? 2) do you have any suggestions for providing fresh air to the furnace? Do you have any other recommendations?
You’re smart to be concerned about providing combustion air to the furnace. I usually recommend that any fuel-burning appliance in a crawl space be a “sealed-combustion” unit that relies on PVC pipes to provide combustion air and vent combustion gasses. If you replace your furnace, definitely opt for this type of furnace, which offers an extra bonus: efficiency above 90%. In the meantime, I think that it would be smart to contact an experienced HVAC contractor and see if he can supply combustion air to your furnace by installing a PVC pipe that extends through the rim joist. If this is possible, you can seal the remaining vents and fully encapsulate the crawl space. Also consider removing the drooping insulation; it’s not doing its job. Installing rigid foam insulation against crawl space walls is the way to go, along with sealing & insulating the rim joist.Good luck.
Hi,
Great information on here.
We live in TN and recently purchased an old farmhouse built in 1902. It has a vented CS with some hanging yellow insulation between the floor joists and some areas that do not have any insulation. I was actually ready to purchase some more insulation to add to the areas that had none before i stumbled upon this website. I would like to use the techniques mentioned here but there are a few issues i’m having. First, there is a porch on the front and side of the house that is open to the CS. So, I’m not sure what to do to make the CS airtight with the porch being part of it. Second, the house is built on a hill; meaning that the front of the CS has a height of about 4ft and it then keeps getting lower as you move toward the back of the house. The very back (about 15ft) of the CS is inaccessible (looks about 5 inches off the ground). The PO had the floor removed to gain access to the back of the CS to run new plumbing. The back part of the house sits on the original stone foundation, as well as part of the sides; it then transitions onto cinder block foundation. Just wondering what my options are as i do not want to remove the floor to gain access to the very back of the house.
You’re facing a challenging situation. You didn’t mention whether or not the crawl space has a dirt floor, but I’m guessing it does. For now, I think you’ll have to settle for partial solutions. Pick the crawl space opening that would be most suitable for access. Build & install a door/cover for this opening that you can seal with weatherstripping and strategically placed screws. Seal all remaining crawl space openings with airtight, insulated covers. Now for the partially accessible crawl space itself. I think for now the best strategy is to insulate as much of the interior wall area as possible, using either rigid foam (extruded polystyrene or polyurethane foam board), closed-cell spray foam, or a combination of the two. Remove & discard the hanging fiberglass. Insulate and air-seal as much of the rim joist (mudsill) area as possible. Installing a thick poly moisture barrier over the dirt floor would also be advisable. Seal this to the wall insulation. If you have water supply pipes in the crawl space, it would be smart to cover them with foam pipe insulation as protection against freezing. At some future time, you may need to open up the floor and do more insulating & sealing. But for now you are new to this old house –still in the discovery phase. See how the house performs after you make these improvements, and go from there. Good luck.
Thank you for the reply Mr.Snyder,
Great advice, I really appreciate it. Yes, its a dirt floor but it already has a plastic vapor barrier. What would be some recommendations to separate the CS area that has porch on top it from the rest of the CS? I was thinking maybe tarps short term, but that might cause condensation issues? I’m guessing building a cinder block wall to separate the areas would be the best option. Thank you again for your advice
ET
ET: Instead of building a cinder block wall to separate the porch from the crawl space, you could frame a partition wall with 2×4 pressure-treated lumber, then cover this framing with a thick poly vapor barrier. Put in a flat, tamped gravel base for the wall’s bottom plate, frame a doorway if you need an access point, and seal the perimeter of the new wall with spray foam.
sounds even better and less work would be involved. I was just worried that the poly vapor barrier would create moisture problems, but i’m assuming that if any moisture builds up it would stay on the side of the poly barrier that’s under the porch. great advice, thanks again
ET
Very useful site – thanks.
My house is a ranch with a basement that is half finished and half crawl space.
We are experiencing real cold temperatures in the main level only in the portion that sits on the finished basement. It’s so bad that even at 60 degrees outside, we have to wear sweaters. At first, I thought it was bad insulation in walls and paid to have walls of main floor and the attic insulated. But it’s still the same so I assume the problem is cold air from the basement coming up the hardwood floors.
Am I right in that? Does cold basement make such a huge impact on main floor?
By the way, the crawl space area is significantly warmer than the finished basement probably because hot water pipes run through it.
So now I’m thinking of carpeting the main floor so that it’s insulated from the basement.
How would I add insulation to the finished basement itself? It’s concrete from outside so don’t think they can spray foam.
Any tips and ideas appreciated.
Thanks
This is a question that was somewhat asked a few times, but I never saw a direct answer to. My question is that when placing down a vapor barrier on the dirt ground where does this align with the ridged foam board?
Vapor Barrier down first, and up the walls a few inches with foam board on last?
Vapor Barrier down first, and then up the walls all the way, with foam board on last?
Foam Board on first, and then the ground vapor barrier up foam a few inches?
Foam Board on first, and then the ground vapor barrier up the foam all the way to the top of the foam?
Side note, is there a good product(s) used for the above process? Its not my intention to use nails or fasteners unless I have to. I’m looking to use liquids, glues, caulks etc… to fasten everything together.
Thank you!
Good question. We’ll address this issue in more detail in a future blog, but for now here’s the short answer. When rigid foam insulation (extruded polystyrene, foil-faced polyiso board or SilverGlo are better than white EPS board) is installed against the crawl space walls (on the interior), joints between boards can be taped to create an air and moisture barrier in addition to a thermal barrier. So when the poly sheet barrier is laid over the crawl space floor, it can lap up several inches onto the foam insulation and be taped to it. You don’t have to extend the floor VB all the way up the walls. The key to success here is to use compatible products –tape, foam, poly VB. It’s critical to use a tough vapor barrier tape that will adhere to the foam and to the poly sheet VB and provide long-term performance under crawl space conditions. One reason that homeowners choose to hire a crawl space specialist (like a CleanSpace contractor, for example) is that they have compatible encapsulation products designed to work as a system. It’s trickier and riskier to assemble these ingredients on your own. I hope this helps.
Tim,
In need of crawl space advise. I’ll set up the situation first, recently purchased a home with a (10′ L x 7′ W x 6′ H) crawl space under the master bath only (was an addition). Being in northern WV, the temps swing from very cold in winter to hot in summer. There are no vents in the CS, but does have a 4′ x 3′ access door. Oddly the floor in the CS is sand (like they intended to pour concrete) and the ceiling has a 3/4″ OSB top and R-19 insulation in between each floor joist of the master bath floor above. We have recently noticed a musty smell in the master bath. Upon investigating, I removed the all OSB ceiling in the CS and some R-19 insulation. The tub above had a leak, which has been fixed. My question is would you replace the CS ceiling with OSB/plywood and the R-19 insulation being such a high ceiling in the CS (making it more like finished space) or attach the rigid foam insulation? Also would you remove the sand floor before adding the vapor barrier to the floor? Your help is much appreciated! Thank you in advance!
Your situation illustrates another disadvantage of insulating the crawl space ceiling: The insulation and OSB concealed a leak that could have been detected & corrected if the ceiling was open. Let’s deal with your CS floor first. The sand layer can serve as an ideal base for a poured-concrete floor, which shouldn’t be costly or difficult to install in this small space. Since your CS has sufficient headroom to be used for storage, a concrete floor would be a real asset. Lay down a thick (6mil minimum) vapor barrier over the sand after leveling and tamping it. The VB should lap up onto your walls. After the concrete floor has hardened, you can trim off the excess plastic.
With a flat, permanent floor in place, you can proceed with insulation & encapsulation. Start by air-sealing & insulating the rim joist. Then insulate your crawl space walls with rigid foam (2-in.-thick extruded polystyrene or polyurethane foam would be best). Leave the ceiling open. If your CS access door is on an exterior wall (as opposed to a basement foundation wall), it’s important to insulate the door with rigid foam and carefully weatherstrip the doorway to seal out drafts & insects. A good carpenter should be able to create an insulated, airtight doorway to your crawl space, even if everything needs to be built from scratch. Good luck.
Tim,
Thank you for your response. I really appreciate it. I’ll definitely implement your suggestion on the rigid insulation instead of the fiberglass batts. I really don’t want to do concrete on the floor due to time, know how and money restraints. In that case would you suggest 1) removing the sand before installing VB. 2) tamping sand then placing VB directly over it
Tim,
Thank you for your response. I really appreciate it. I’ll definitely implement your suggestion on the rigid insulation instead of the fiberglass batts. I really don’t want to do concrete on the floor due to time, know how and money restraints. In that case would you suggest 1) removing the sand before installing VB. 2) tamping sand then placing VB directly over it
John: Don’t remove the sand; it will help protect the vapor barrier from rocks in the soil that might puncture the barrier. Level & tamp the sand, removing any protruding rocks as you go. If you’re going to insulate the walls, install the rigid foam after air-sealing & insulating the rim joist. Then lay a thick, durable poly sheet over the CS floor, lapping the edges up onto the foam wall insulation. Tape the poly to the foam boards, and make sure all joints between foam boards are sealed with tape (spray foam the gaps, too). That should do it (providing you didn’t leave out insulating & weatherstripping the CS door.
Hi, Tim. Thanks for a great website and sharing your information.
My son bought a 1970s frame ranch in Cleveland, OH two years ago and encountered a sinking 10’x20′ room addition that was built on 5 PT piers with insufficient footings. This week a contractor is jacking and leveling the addition and adding proper footings under the piers but my son and I need to address the following issues afterward. There is black poly on a dirt “floor”, no water problems, and one flex heating duct. The addition’s plywood sheathing extends to the ground but needs to be replaced w/ something suited for exposure to the ground and ongoing critter problems (racoons, groundhogs, and skunks so far- ugh). There is low clearance maybe 12″-18″‘ between ground and bottom of joists but we can probably access most/all of the addition’s rim joists / perimeter.
1) Should we build a wall with 2×4 PT framing mount to rim joists and extend below ground to a gravel base per your response in #49 above? How deep should wall extend below grade to deter critters?
2) What would be a good material to mount on frame that can be at/under ground, keep critters out, and serve as a backing for an aesthetic finish (faux face brick)?
3) The flex ductwork needs repair or replacing due to critters. What is best ductwork for this type of CS? I presume that we should try to get duct off ground and mount between a joist but if we can’t get access is there a way to optimize ductwork in this situation? We could pull back carpet and remove a section of subfloor to redo ductwork if necessary.
4) Given low clearance what is best way to insulate this CS? Rigid insulation laid on the ground over poly? Remove subfloor and insulate from above?
Hi Mark,
I’m glad you’re giving your son a hand with his house. Your description leads me to believe that whoever built the addition used shoddy construction techniques. Let’s try to correct them. Since the contractor will need to do some digging to put in proper footings & piers, I suggest that you take this opportunity to create a little more access space beneath the entire crawl space. It’s important to get underneath the addition for several reasons: 1)totally clean out nests & debris from between joists; 2)inspect overall framing to check for mold & rot; c)air-seal & insulate; d)upgrade ductwork.
It will be too expensive to transform a pier foundation into a proper crawl space, so I suggest that you take steps to turn the addition’s floor into the thermal & air boundary. Replace the flexduct with sheet metal ductwork that’s up off the ground and can be sealed and insulated. Use spray foam to air-seal the sheathing & rim joist from below. Cut rigid foam to friction-fit between crawl space joists, then seal along the edges with spray foam. I recommend 4 in. of foil-faced polyiso board (you’ll probably have to buy thinner polyiso board and install a couple of layers.). Once this insulation step is complete, screw 1/2-in.-thick exterior plywood to the bottom edges of the joists to keep critters & insects out.
Now for finishing the perimeter. Several options here. You might consider framing a p.t. lumber wall, with the bottom plate about 12 in. below grade. You could staple aluminum screen (hardware cloth) to the outside of the wall, and then install vinyl lattice over the screen. The screen will keep out insects & animals; the trellis improves appearance & strength. I’d favor this approach over building a solid wall. Good luck.
Good afternoon, great website for info. I have a question, hopeful to get some feed back. Im in New York City. I have a crawlspace over two bedrooms. Just about at ground level. The crawl space has a cement floor with brick walls. The space is about 26 feet wide by 15 feet. But the problem is that theres only about 18 inches of space between the crawl space floor and the joists holding up the flooring for the bedrooms. Not enough room to get myself under there. Seems like spray foam is the only option. Should I request open or closed cell from the spray foam company?
Greg: You didn’t mention if the brick walls of the CS have vents or not. I’m going to guess that they do. I would suggest having a spray foam specialist coat your rim joist and crawl space walls with 2 in. of closed-cell spray foam. Also install insulated, tightly weatherstripped covers on all vent & CS door openings. Good luck.
Thank you for getting back to me. There are no vents anywhere in the crawl space.
Hello again,
After doing more research and contacting some local contractors I have come across some contradicting advice in my area (Mid Michigan). I was recently told today actually, by a contractor that was willing to encapsulate my crawlspace that no insulation would be needed on my crawlspace walls. 40″ deep crawl space. Maybe 6″ of it is above grade. He would simply place down a 20 mil vapor barrier all along the floor and up the walls. They would also seal and insulate the rim joist in the entire crawl space. The method of thinking on this is that the blocks below grade would make the insulation cold therefore what am I really insulating? They would also tap into my HVAC system and that is how I would have the air conditioned for the space. Possibly, a dehumidifier down there if needed. But I was more than surprised to hear that they did not plan on putting any insulation along the wall. He said he gladly would if I wanted to but does not see the need for it.
I’ve been in many, and lived in a couple houses with a block basement with no wall insulation. MAYBE got down to 55* in dead of winter. So I can see that method of thinking if I look that direction.
Long question short is that now I am contemplating if insulation on the walls is truly necessary? As long as I have a good vapor barrier and my rim joists are properly insulated and everything is closed off to the outside, am i safe enough as it is? Or is it smart spending the extra money for the ridged foam board insulation? Also factoring in the time it would take to recoup that cost on heating bill.
Hope all that makes sense, thank you in advance!
Hi Tim, great website. I have 24 X 24 crawl space with wood foundation walls about 4′ high. My question is how I should insulate and seal the wood walls. They seam to be fairly dry but the dirt floor being a little damp. Was going to foam the walls but sounds like a bad idea.
Gary: Any wood in direct contact with the soil will rot unless it’s pressure treated. I would suggest pressure-treated framing near ground level and exterior cladding (sheathing and/or siding) that can’t be damaged by moisture –composite or plastic boards. Air-seal and insulate the rim joist carefully, using a combination of 1-part spray foam and rigid foam board. This same technique will work for insulating between the studs of your crawl space wall.
Tim,
I live in Portland Oregon. Not too humid up here. I recently bought a home and the contractor who did the remodel replaced about 85-90% of the insulation in the crawlspace. They also put a new vapor barrier down. The vapor barrier could use some help on the walls but over all it looks pretty good. The crawl space is very dry. I have spent some time done there doing some duct repairs. My concern is the way the insulation is held up. They stapled vapor barrier to the joist to hold up the insulation. I have seen this a few times but am unsure about it. What are you thoughts on it?
I like the idea of full encapsulation but I feel that since this has all been done in the last few months. I don’t want to spend a bunch of money replacing it right away when I can wait a bit and get the use out of whats down there.
Thanks!
Hi Jacob,
Your query leaves out some important details. I’m assuming that fiberglass batt insulation has been installed between joists, and that a plastic vapor barrier was stapled along the bottom edges of joists. There are certain to be energy-wasting leaks in this thermal & air boundary –like where plumbing, electrical and ductwork extend up through the first floor. I would take care to seal those areas carefully, and just live with the system for a year. Keep track of where floors feel cold, and note how moisture levels change over time. You probably have ductwork that’s located below the insulation, which means that in winter you’ll be blowing heated air through cold ducts –not good for economy or comfort. You could add duct insulation or wait until you can encapsulate your crawl space and insulate the foundation walls to put the HVAC system inside the building envelope. Good luck.
Tim
Yes there is standard vapor barrier on the crawl space floors and up the walls. Then there was additional vapor barrier stapled to the floor joists to secure the insulation instead of string or chicken wire. The insulation is standard fiber glass.My main concern is that th plastic against the insulation will condensate and lead to mold issues. I have asked around the area and most insulation installers do not recommend having the plastic secure the insulation. Thoughts?
Thanks,
Jacob
Great topic, seems like this is effecting a lot of people.i have a crawl space that had encapsulated and insulation form fitted between the joists. I didn’t insulate the walls because the contractor wanted too much for that step for my liking. Can I apply the foam boards myselfon top of the encapsulation material with an adhesive or should I pull it off and apply direct to foundation.
Thanks for all the info!
Mike
Mike: With your crawl space ceiling insulated, you’ve established the thermal boundary at the bottom of your living space. You don’t want a second thermal boundary against the foundation walls. So if you want to add insulation, it should be in the form of rigid foam panels that are fastened against the bottom edges of joists in the crawl space. I suggest foil-faced polyiso board in 1.5-in. or 2-in. thickness. Seal the joints between panels with aluminum tape to create a tight air barrier. Good luck.
Tim,
Thanks for all the great info. Our home is located on the south shore of Long Island,N.Y., about a mile north of the coast. It’s a cape built in 1932 with an unfinished basement, there’s a 12×28 extension off the back with a 30 inch high crawlspace. The crawl was built in two stages, the first half in 1945 and added to in the 80’s. It’s a block foundation with no vents; the only access is from outside under the rear steps, a 24×30 plywood panel with some holes drilled through it ( for ventilation?). The original half has R19 fiberglass batts attached to the sill plate with furring strips, running from against the rim joist down the wall to about 24 inches laying on the floor. The dirt floor has a plastic vapor barrier, not seam sealed or adhered to the walls. The joist spaces are open. The rear half has a rough concrete floor, no visible vapor barrier and R19 batts in the joist spaces. The room above has radiant heat panels on top of the subfloor, only penetrations are for pex tubing and wiring. My original thinking was encapsulation because it has been relatively dry down there, as far as I know. But recently I was down there in the older half running a cable for my son’s computer and found a small puddle of water on top of the vapor barrier and some of the batts wet at floor level. I think it may be from the heavy rains we had in August (13″ in 24 hrs.) which resulted in the worst flooding we’ve seen since we’ve been here, 1990. Did not see any leaks from above. I’d appreciate your thoughts on the best way to insulate and seal the crawlspace; thanks again for your help. (Sorry for being lengthy, just tried to be detailed).
Rich: No need to apologize for the long description; these details help. I’d recommend fully encapsulating your crawl space. See my blog about handling the crawl space floor to evaluate your options there. If you only had a small amount of water on the floor after that amount of rain, I don’t think you need a crawl space sump pump. However, it would be wise to create some drainage & drying space beneath new, fully sealed, continuous floor moisture barrier you’re going to install. The dimpled plastic sheet material mentioned (and shown) in the blog works well. 3/4-in. or 1-in. gravel will also work. Remove the fiberglass insulation that’s draped down the walls. Carefully seal & insulate the rim joist with rigid foam and spray foam. Install rigid foam insulation against the block walls (I’d recommend 2-in.-thick extruded polystyrene). You can leave the ceiling fiberglass in place if it’s in good shape and not hiding pests; otherwise, take it out. Finally, upgrade your access door so that it’s airtight (use weatherstripping where the door frame meets stop molding) and insulated with the same rigid foam. Since you won’t need to get into the space often, I’d just screw the door shut. Hope this helps. If you get this work done now, the living space above will be more comfortable this winter.
Tim-
Thank you for your response; could you tell me where to find the floor options info?
Also, do you think the 2″ rigid foam is enough R value? Just want to get it right and do it once. Thanks once again for all your help.
Tim,
We recently bought a home that was built in the 1960’s, there is a vented crawl space that has r19 insulation installed. Would it be ok to install Ecofoil directly underneath the fiberglass insulation, or does the fiberglass have to be removed first?
Scott
Scott: If you want to keep using the crawl space ceiling as your thermal & pressure barrier, keep the fiberglass insulation in place. I would prefer to install 1-in. thick (or thicker) foil-faced polyiso board against the bottom edges of the CS ceiling joists, but if you’re set on the Ecofoil, it can be stapled against the bottom edges of the studs. Unless you seal all foil edges with Ecofoil’s special tape, you’ll still be allowing cold outside air to enter the floor assembly and chill your floors.
Thanks Tim. If I do decide to use the foam board, do I need to install a thermal or fire barrier?
Thanks
Tim, my wife and I live in Charleston, SC and recently had our crawlspace sealed and a dehumidifier installed to help control the humidity and stop mold growth. Unfortunately, the damage was done. As soon as we closed off the crawlspace we noticed a “not so nice” odor that coincided exactly with the dehumidifier cycle time. We have since determined that there was quite a bit of mold growing under the house and the contractor simply encapsulated the crawl space without notifying us of the mold issue and without removing the old, moldy fiberglass insulation. My wife and I decided to tackle the project as a DIY project; we simply have lost confidence in the local contractors’ abilities to do quality work. Anyway, we have no removed all of the insulation and I am wondering if we even need to replace it? Can I simply install insulation rigid foam insulation along the perimeter walls per your instructions in previous posts? It would definitely save us time and serious bucks. Thanks for your time!
Hi Karl,
You’re right: Your contractor should have alerted you about the mold before encapsulating the crawl space. Don’t replace the fiberglass insulation you removed from the crawl space ceiling. Instead, I recommend installing rigid foam (1.5-in. or 2-in. thick) against the crawl space walls. But before you do this, it would be wise to let your dehumidifier do its job for a couple of weeks. Masonry foundation walls and wood framing & sheathing can store a great deal of moisture. Now that your crawl space is sealed and no moist air can enter from outside, getting the space dry is a priority. A good dehumidifier should be able to remove moisture that has accumulated, and this is the best way to create a mold-hostile environment –just what you’re aiming for. Insulate the CS walls with rigid foam after you’ve dried out the space. Good luck.
Tim,
Thanks for the quick response, and exactly the response I was hoping for, too. I am pretty sure we’re going to do a little mold remediation down there before buttoning it back up tight, so we’ll definitely take your advice and let the dehumidifier to its thing. My wife is leaning in a green direction for mold remediation and plans to use a tea tree oil treatment. Any advise on that front before I pull the trigger? Once again, thanks for your time.
Karl:
Be careful working around mold, especially within the confines of a crawl space. An effective respirator is essential to filter out airborne spores. The realistic approach is to kill as much visible surface mold as possible and then dry out the space to make it difficult or impossible for mold to grow.
Tim, I have a crawlspace with a dirt floor covered with thick plastic, in Central Tennessee, the walls are bare and there are not bats in the floor joists. I am considering denim insulation bats (R30) in the joists. Is this a good or bad idea? Thank you for your time on this Tim, I don’t want to purchase something if it is not going to keep the floors warm in the winter.
The crawlspace is vented, I left out that detail, the denim batts I am considering were decided upon because there is no fiberglass to contend with and their recycled nature, the are actually made of recycled denim jeans and jackets, etc.
The composition is recycled fiber products, boric , ammonium sulfate, and binder fiber.
It contains no fiberglass, asbestos, or formaldehyde.
Hi Roy,
Denim batts can definitely be considered a “green” insulation, but I don’t recommend using them in a vented crawl space. Here’s why: At certain times of the year, you’ll have warm, humid air entering the crawl space through your vents. When this outside air cools in the crawl space, it will give up its moisture –you’ll have droplets of condensation forming on cool surfaces like joists, nails and sheathing. Denim batts will soak up this moisture like a sponge, losing their R-value and creating wet conditions favorable to mold growth.
The better strategy would be to install 2 in. of rigid foam insulation against crawl space walls (from inside the CS), air-seal & insulate the rim joist and seal up the vent openings with airtight covers. Make one of the covers removable for CS access. Create a continuous air & moisture barrier on the floor by taping the poly floor cover to the rigid foam wall insulation. If your crawl space already has moldy, damp wood, you’ll need to run a dehumidifier after sealing the space to dry out the space. Once the space is dried to above 50% RH, you can stop running the dehumidifier, and keep the CS sealed up.
I have been reading through the posts and found a lot of information. We are thinking of buying a 1890 cottage in the Northeast, near the beach. No heat, no insulation and no laundry room! Wood flooring, vinyl siding and oh yes, and a crawl space. What is the best way to get information on how to best winterize year round given all the green tech in 2014 and how much each improvement will cost actually?
thank you
Check the real estate listing for the house you’re looking to buy. If the house is in a flood zone, requiring flood insurance, then this will have a bearing on how you handle the crawl space. Instead of encapsulating the crawl space, it would be better to install flood vents in the CS vent openings, so that flood water can flow through the foundation rather than beat against it. With this approach, you would need to air-seal the CS ceiling and insulate it.
If you’re not in a flood zone, opt for CS encapsulation as described elsewhere on this site. Good luck.
Tim,
I live in a house built in the late 1930s. I have a vented crawl space, and by vented, I mean open holes in the side of the foundation. I’ve read through most of the responses here, and I really didn’t see something that would apply to my situation..
The crawl space is extremely small, rough guess, the most space I have between the joist and the ground is 12″ with most of the space much less. I don’t think it would be possible to insulate the inside wall of the CS. I do plan on knocking out the current vents and replacing with standard vents that can be opened and closed. What do you suggest for the rest of the foundation?
It’s difficult to make a helpful recommendation without knowing where your house is located. It would also be good to know whether you have masonry or wood-frame walls, and what kind of heating system you have. Please provide a few key details as I’ve suggested.
The house is located in East Tenneessee. Wood frame home with a cinder block foundation. Heat pump has been installed, with all the ductwork in the attic. Single story home of about a bit over 1000 sq. ft. 9 ft. ceilings. Windows have been replaced with new double panes windows.
When a crawl space is too shallow or cramped for safe access, there are still some insulating options, but they tend to be tricky, expensive or both. One option is to dig a trench around the outside of the foundation and insulate the exterior walls with 2-in.-thick extruded polystyrene. To avoid trapping water above and behind the rigid foam, you’ll have to take special care with sheet metal flashing that tucks under the siding and over the top edge of the rigid foam. Tricky, but effective in keeping out the cold. The trench provides a good opportunity to improve draining by installing drainage tile –a nice side benefit. Make sure to close all vents in the CS walls and to make the CS access door as airtight as possible. Good luck.
Hey Tim,
I have been reading through the posts as well as other websites and am getting mixed messages. I have a 1942 brick bungalow in Jacksonville, FL. The crawlspace is earth and the floor is between 2′ and 4′ above grade. (there is a slight slope). The foundation is brick on top of concrete footers and has numerous vents all round that are vertical slats in the bricks. The house above is wood frame with brick veneer. Crawlspace only contains plumbing, HVAC and ductwork are in the attic. No flooding problems due to elevation.
When it is cold here the floor feels very cold and the heat runs alot. I have gotten an estimate for insulation under the flooring between the joists. They are proposing fiberglass batts with the paper facing upward toward the subflooring. Now to my question. Some locals say that this will cause moisture to develop under the subflooring especially in summer when the house and floor are cooler than the warm humid air in the crawlspace.
Would it be more advisable to put some kind of insulation against the walls and close off some of the vents (there are alot of them, too many I think.)
Thx…John
John: Your friends are right about summer moisture problems. When warm, moist outside air enters your crawl space, it will condense on cool surfaces (floor sheathing, floor joists, copper pipes, etc.). You’ll have ongoing moisture problems. If you’re serious about improving comfort and avoiding moisture problems, I’d recommend installing rigid foam insulation (2-in.-thick extruded polystyrene or SilverGlo(r) panels) against your CS foundation walls (inside the foundation). You can run the rigid foam right over the vent openings so that they’re sealed off as well. Make the CS access door as airtight as possible by installing foam weatherstripping and latching or screwing the door fast. Air-seal and insulate the rim joist. Install a poly moisture barrier over the dirt floor, taking care to tape all seams, and to tape the poly to your wall insulation. All of this work is standard for experienced CS contractors like those in the CleanSpace network.
Tim,
Thanks for this piece. I have a general question about insulating a crawl space on the inside. Doing so will obviously make the exterior faces of the crawl space walls much colder in the winter. Will the resulting increased exterior freezing and thawing gradually cause damage to the foundation? This seems like a potential unintended consequence worth considering, so I was wondering if any research had been done on it. We live in central Illinois, and even with regrading the water content of our heavy clay soil is pretty high.
By the way, we would probably use cellular glass insulation or AirKrete instead of plastic foam, in order to avoid the flame retardants and other environmental negatives that go with plastic foam. I think these are good alternatives to consider.
Hi Charles,
Expansive clay soil can wreak havoc on a foundation regardless of insulation status. Definitely take care of this issue by improving drainage around the foundation and by replacing clay-rich soil adjacent to the foundation with more permeable soil that doesn’t expand & contract so significantly.
As for your plans to insulate CS walls, I wouldn’t be too concerned about outgassing or environmental hazards of rigid foam insulation like extruded polystyrene. As you know, green value also has to do with durability & maintenance. Rigid foam is inert and permanent; it won’t degrade, lose R-value, compress or displace like fibrous insulation can. It will probably be less expensive to install than AirKrete. Whatever treatment you choose, make sure that it includes air-sealing & insulating the rim joist as well as foundation walls, sealing vents, and installing a moisture barrier over the CS floor. Good luck.
I am actually not really concerned about soil expansion, as the foundation shows no signs of cracking or stress (with one exception, clearly due to a tree) in the 50 years the house has been standing, in spite of the fact that the grading around it was much worse than it is now for most of that time. I suspect this is because the foundation was laid when the soil was fairly saturated. In drought periods, the soil pulls away from the foundation, and thus it seems not to create excessive pressure when wet. (We are careful not to push any soil into the crack when it is dry, and I was careful to maintain this equilibrium when regrading to create a better slope away from the foundation.)
So my question was really about water getting into the concrete or mortar by capillary action and freezing. I noticed, for example, that there was damage to some joints above ground where vegetation had led to moisture accumulation on the North side of the house (problem since fixed), but the underground surface of the foundation below this area looked perfect. A neglected downspout that drained toward the foundation actually created a hole in one of the cinder blocks under the outer wall of the garage, which has a slab floor, so the wall is not warmed by escaping heat from the house. (That problem is also fixed, but I still have to replace the block). These observations, particularly the moisture damage to the above-ground foundation, which gets colder than the part below the ground, led me to wonder if anyone had studied what might happen to the exterior surface in general on account of its being colder after insulating, since water can clearly infiltrate the minute fissures in concrete.
Thanks for all your advice, and in general for creating this site!
I recently purchased a home in Sullivan County NY. It’s a split level and the crawl space floor is one with the finished basement. There is no insulation of any kind in the CS so I am grateful for all of the information. Can I just insulate the walls and joists without putting anything on the cement floor .
Start out by air-sealing and insulating the rim joist. Then insulate the crawl space walls with rigid foam. You may find that this improves your comfort enough, so that floor insulation isn’t necessary. It’s good to note how your home behaves after an energy-saving upgrade. If there are still parts of your floor (above the crawl space) that are cold, this tells you that more insulation or air sealing is necessary somewhere.
Re Insulating crawl space – live in Canada – addition on piers, dirt floors, no solid walls.
Can you tell me if I should use fiberglass bats between the joist before sealing with polyiso across the bottom of the joists. also have put vapour barrier on floor
With an open pier-and-beam foundation, the floor framing will be where you create the thermal and air boundary. The first thing I would do is use canned spray foam to fill & seal all penetrations in the floor to bring wiring, plumbing & ductwork into the living space. Then install unfaced fiberglass insulation to the full depth of the joists. Finish up by installing rigid foam insulation against the bottom edges of the joists, taking care to seal all joints between panels. Foil-faced polyiso board or extruded polystyrene are preferable to white EPS foam.
Thanks for such a quick response Tim. Do you recommend Roxul of Pink insulation bats?
Gerry: Roxul is more expensive, as you probably know. But it tends to hold its shape better than fiberglass. I think either will do. If it were my house, I’d probably score some savings by installing the fiberglass batts, and use the savings to up the thickness of the rigid foam –let’s say 2-in.-thick rigid foam instead of 1 1/2-in.-thick foam.
Tim
would it be safe to put stapled down hardwood flooring in the room above after I have done the insulation/foil back polyiso in the crawl space?
Tim,
If your crawl space is in a flood zone, will polyiso have to be removed from the masonry crawl space walls if flooding does occur?
Polyiso board and extruded polystyrene rigid foam should be able to withstand full immersion without deteriorating. Removal shouldn’t be necessary. However, it’s possible that some rigid foam panels may break loose from walls and need to be reattached.
Great article. Excellent information. Perhaps you can help with my situation.
I have two crawlspaces from additions that were added to the house for previous owners. They have no vents to the outside. They actually sit about 4 feet above the rest of the basement. They are both dry and over the last year and a half have had no signs of water in them. They are fully open to the rest of my basement. The foundation is concrete block throughout the entire basement. There is a poured concrete floor in each crawlspace. There is a radon mitigation system with pipes coming from the main section of the basement as well as each crawl space. I’ve tested the radon levels and it seems that all is functioning well. Last year I used 2 part closed cell spray foam on all of the rim joists 2 inches thick and added r30 un-faced on top. (overkill, but the Mrs. doesn’t like to be cold)
I intend to insulate the crawl spaces with 2 inches of foil faced foam, tape seams, etc. My question is with regards to the floor. Do I have to put down poly on the floor? Radon mitigation is already in place. Moisture doesn’t seem to be an issue and it’s fully open to the rest of the basement. Could I just put the same foil faced insulation on the floor of the crawl spaces and foam the joints where the floor meets the wall? Or as a second option could I use a product like Amvic Amdry on the floor of the crawl? It’s like Dricore but with 2 inches of foam insulation. It would also provide some air movement underneath for moisture that did work it’s way up from the ground. I appreciate any response. I can’t seem to find a definitive solution for my situation. Most instructions for insulating crawlspaces are for people with dirt floors.
Patrick: You’re fortunate that the crawl space additions were built without vents and with poured concrete floors. Since there doesn’t seem to be a moisture problem in the crawl spaces, I think you could insulate the CS floors with extruded polystyrene rather than with foil-faced polyiso board. The extruded polystyrene panels are a bit less expensive than the polyiso, and no less waterproof.
If budget is a concern, you might consider spending the insulation money on rigid foam for the basement walls instead of for the CS floors. This is likely to provide more comfort & energy efficiency benefits than the CS floor insulation. If you basement already has finished walls, this option won’t be available. But if the bare concrete walls are still exposed (and sucking heat from your living space), I would insulate the basement walls before doing more in your crawl spaces. Good luck.
Thanks for that response. Great advice. One last question… When insulating crawlspaces and basements do you insulate the floor first or the walls first? i.e. Should the foam against the walls rest on top of the foam placed on the floor?
Thanks again. Great site.
Hi Tim, thanks for the great website and advice. Here’s my question. I live in cold NJ in a 1940 balloon framed two story house. I have a full unfinished basement with concrete floor but I have two crawl spaces at opposite ends of the basement. One that is 4 x 10 unvented with a dirt floor under our kitchen and another crawl space that is newer and about 10 x 10 and vented on two sides with a concrete floor. Both crawl spaces are 3 or 4 feet above the rest of the basement floor with small doors to climb in so they have never had moisture problems at all. I want to condition both these rooms for the sake of cold air coming through our upstairs floors. First, can I level the small dirt floor and lay 2″ rigid foam board right on the ground or do you still recommend vapor barrier underneath it and against the walls before attaching the foam board? What is the best way to attach vapor barrier to the concrete walls? How about attaching the foam board to the walls and floor? Also, would I use spray foam at the top of the foam board where it meets the sill plate in order to seal it? If this works out easy enough for me in the crawl spaces, I will continue to foam board the rest of the basement walls which are cinder block and not in as good a shape. Thank you for your response!
Dale: First I would air-seal and insulate the rim joists in both crawl spaces and the basement. This can be done with a combination of friction-fit rigid foam (between joists) and spray foam around edges and in gaps. Then install rigid foam insulation against CS walls; I’d recommend 2-in.-thick extruded polystyrene or polyiso board. You’ll also need to permanently seal & insulate the CS vents. You may be able to adhere rigid foam to walls with construction adhesive, but if the masonry is really dirty and dusty, you’ll have to secure panels with adhesive and masonry fasteners (just 2 per panel should do it).
Definitely lay a thick poly moisture barrier over the dirt floor. Lap the edges up onto the wall insulation, and seal the joint with compatible tape. After these improvements, you may discover that no further insulation is necessary. But if it’s still cold upstairs, consider replacing old basement windows or installing basement wall insulation before insulating the CS floors. Good luck.
Tim, I have been reading that when using foamboard in your rim joists or basement walls, you need to afterward cover the board with fireproof drywall. When I added pieces of rigid foam to my rim joists, I sealed around the edges with a bit of spray expanding foam. Now does the drywall covering have to fit perfectly snug in those rim joists because Im finding that every single one of my 35 joist areas measures different by 1/16 to a few full inches. It is a lot of precise measuring for someone with intermediate talent. Also, I am having trouble finding the recommended 10-12 mil plastic sheeting for my small dirt floor area. Would it be just as good to layer two 6 mil sheets that are folded over? Thank you.
Hi Tim – Thanks for the very informative post!!! Real quick (probably naive) question: How do I mount the rigid foam board to the crawlspace wall? I live in northern NJ… probably have a fairly typical crawlspace – floor is concrete and walls are block.
Thanks in advance!
Steve: If the interior block surface is clean and dry, a you can adhere rigid foam to the foundation wall using a compatible panel adhesive. But adhesive alone usually isn’t enough, for several reasons. First of all, crawl space foundation walls are rarely sufficiently clean and dry. Secondly, temperature and humidity conditions may not be favorable for best adhesion. The answer: Combine your panel adhesive strategy with some specialized plastic fasteners that have barbed shanks and washer heads. One source of supply: http://rodenhouse-inc.com/products/plasti-grip-pmf-plastic-masonry-fastener/
Just 2 or three fasteners per panel should be sufficient. If you can’t use these fasteners, I’d go for Tapcon screws with fender washers. Good luck.
My situation is a combination of many others discussed earlier. I live in a log home built of re-purposed logs and barn timbers. I have about 1200 sq ft of crawl space plus a heated, unfinished basement. The perimeter of the crawl space consists of cinder block walls. About a third of the walls form the external walls of the basement (concrete floors), and the rest face outside. Two access doors made of barn boards. The crawl space is vented to the outside without mechanical assists. I have the now-dreaded bat fiberglass insulation between floor joists. Yep, they are hanging to the ground in several places (They gave out over a span of 35 years!). There are signs of mold on the floor joists. Also evidence of mice dwelling in insulation. No visible moisture problem otherwise, as the bare ground of the crawl space is dusty dry. Even so, there is the mold.
About a year ago, I installed new hardwood flooring to replace carpeting. The carpeting, padding, particle board underlayment, and sub-flooring (1X6″) showed no signs of moisture, rot, or insect damage. Very dry all around. However, I’m concerned to protect the new wood flooring, get rid of any signs of molding, increase the comfort level of the house in general, and do what I can to conserve energy. I’m ready to make proper changes to the crawl space without spending another fortune. All suggestions welcome. Thanks!
Hi John,
Sounds like you’ve got a “classic” vented crawl space that needs to be encapsulated. Remove the fiberglass insulation and do your best to clean the entire space. If you just have surface mold on joists & other wood in the crawl space (rather than wood rot that may indicate structural issues), this can be treated with a bleach solution. It will be necessary to air-seal the rim joist with spray foam, and insulate your CS walls with rigid foam. Seal the vent openings with plywood covers, rigid foam and spray foam (to create an airtight, insulated barrier), and spend some time transforming (or replacing) your CS access doors to insulated doors that can be made more airtight with weatherstripping. Place a poly moisture barrier over the floor, lap the poly onto the foam wall insulation, and tape the joints with compatible tape. This is a substantial amount of work, so you might consider contacting a CleanSpace dealer in your area before going totally DIY. Good luck.
Where can I buy TerraBlock insulation for placing on my crawl space dirt floor in the northern Michigan area? I am installing drain pipe around the perimeter footings and across the center to drain into a sump crock to get rid of the ground water..
With water issues and a dirt-floored crawl space that needs not just insulation but good drainage, I suggest finding the nearest CleanSpace dealer. Call 1-800-638-7048 to get some professional assistance (including access to these special products).
Tim,
I have a home in Ocean City NJ that has a crawl space with vents. There is a vapor barrier but no other insulation. The previous owner utilized base board heating for the house and heated the crawl with 2 fin tubes to provide protection from pipes freezing. Unlike the previous owner I do not live in the house in the winter months. I just recently switched the heat over to forced hot air so I don’t have to worry about the baseboard heat popping a leak while I m not there. My problem now is that I am at risk for a frozen pipe in the crawl space because the 2 fin tubes are no longer functioning because I dismantled the base board heating system. There is no way to add heat to the crawl space via the forced air system as all the ducts originate in the attic (that is where the air handler is located). From reading the various post here I am guessing the best option is apply closed cell spray foam to the walls. Close the vents in the winter and seal them with rigid insulation. I would then open these vents in the summer months. Would there be any benefit to spraying the crawl space ceiling too with spray foam? Or should I just invest in heat tape for the pipes? I am not a DIY type of guy so I will be hiring someone. I am not as concerned about cost as I am about having it done properly. Thank you in advance for your reply
I suggest contacting a contractor who specializes in crawl space encapsulation. If there’s a CleanSpace dealer in your area, that’s an excellent place to start. Call 1-800-638-7048 to locate a nearby contractor. Either closed-cell SPF or rigid foam will work to insulate your crawl space walls. It’s also critical to seal & insulate the rim joist area. You may want to wrap the supply lines in your crawl space with heat tape as a failsafe measure, but the insulation & encapsulation improvements will probably provide adequate freeze protection. I don’t recommend opening the vents during the summer. This will allow warm, humid air to enter the crawl space and then condense on cooler interior surfaces, causing a number of moisture problems.
Tim,
thanks for the advice above….i did have 3 contractors come out to look at my crawl space. Contractor #1 provided an estimate for a proprietary vapor barrier that was the equivalent of 15mil thickness. It would have taped seams and be fastened a least 6″ up the wall. He also recommended 2 dehumidifiers. They do not provide insulation services. The 2nd contractor provided an estimate for both vapor barrier and spray foam insulation on the wall and rim joist. His vapor barrier was a standard vapor barrier 6mil thick with seams to be overlapped by 12 inches but not taped. The 3rd contractor utilizes a vapor barrier called Silver Glo which would have taped seams and was around 9mil thick. He would then use either foam board on walls and spray foam in rim joist or spray foam both walls and rim joist. Contractors #1 and 3 were approximately twice the price of contractor #2 with the only difference being in the vapor barrier material. I could have contractor #1 install the vapor barrier and have contractor #2 do the insulation but I really wanted to use 1 contractor. My question is….are you ok with contractor #2 and his vapor barrier method?. Lastly, the house is in a flood zone but has only experience a few inches of water once in 28 years and that was during Hurricaine Sandy. I plan on sealing the crawl space vents. Thanks in advance for your response.
Hello mates, how is everything, and what you would like to
say about this article, in my view its genuinely amazing in support of me.
Hi Tim,
I live in Arizona and my home was built in 1890s. Its adobe and one of the oldest homes out here. It also has a dirt floor crawl space with vents. Am I correct in assuming encapsulation applies here too? My crawl space is pretty small and I’d really like to dig it down another foot or two before encapsulating. Can I create a vapor barrier beneath the first floor, excavate (will require water as dirt floor is hard/dry) then encapsulate?
I have a crawl space that approximately 15” in height with a dirt floor. The sump pump is set up outside, yuk! It’s always wet down there. I live near Chicago and was told putting drain tile around the outside is my only option. The dehumidifier idea sounds good excep there’s no way toputitin the crawl space because no one can get in there because of the height. There is an access door in the utility room, but that doesn’t help anyone gain access. When there’s a really heavy rain the water has come close to the floor. Any suggestions would be appreciated.
Should the foam board insulation go all the way to the ground? I understand there should be space at the top of the wall uncovered for termite inspection, but unsure how far down to run the foam board.
Thanks
I just paid $600 to remove all of the foil-backed fiberglass insulation from walls of my enclosed crawl space which was hiding termite tunnels. Exterminator (O….) cautioned against using foam (board or sprayed) to re-insulate as termites go right through it on the way to find wood. I would minimally leave a 3-6″ inspection break between foam and first occurence of wood but would still the risk of having to tear out the foam if termites were found in the future. Seems like the only safe way to get away from termites is to build house on steel stilts, all metal framing, cement board siding! Good grief. And, I just had a neighbor completely encapsulate his crawl space–not cheap. But it would make termite inspection/treatment impossible without tearout.
Hi! I have a crawl space and my feet get cold in the winter. The crawl space is vented and I am not interested in encapsulation due to the high cost. I will air seal as best I can with foam spray. One room in the house is much colder in the winter and much hotter in the summer than the rest of the house. Will air sealing and applying foam board between joists under that room ONLY affect the environment of that room?
Tim, just happened on ur article by accident, but here is my problem, inherited a 1938 built house in central area of NC, we have sandrock here, ie, doesn’t absorb water(don’t perk etc.)small house with water under topsoil. have dug ditches and r presently draining, CS has had water on top of existing heavy clear plastic, yes I know french drains r in order on outside high slope to house. we just tore out old bathroom floor and rebuilt from foundation up to walls, yes they were rotten and water damaged from leaks. as moisture is a problem what is your advice to insulate ceiling of CS, floor in bathroom very very cold, oh is open on east end, will be purring cinder block wall up when finishing up bathroom project.
thanks, Jean M. High Point NC
I have a cottage on piers which had a incorrectly insulated crawl space. All existing fiberglass has been removed and damaged wood replaced. I am considering construction of a concrete block curtain wall around the exterior to replace existing wooden panels. At the same time remove any soil overburden from the granite bedrock under the cottage. Then spray foam closed cell over walls and granite ground to create encapsulated space. The crawl space is not used for storage and has no openings to interior of cottage. Cottage is located on Lake Huron. Do you see any problems with this plan?
Do you have a spam issue on this site; I also am a blogger, and
I was wanting to know your situation; many of us have created some nice procedures and we are looking to
trade solutions with others, please shoot me an email if interested.
Hi Tim,
I took the fibre insulation bats out of my crawl space and had the walls insulated with spray foam. I did not have a proper perimeter drainage but that is done now as well. The crawl space floor is rough concrete.
I sealed off the wall vents but the moisture in the crawl space is still in the high 70. I used a benefect product on the wood works to kill mould and mildew. Would it help to insulate the concrete floor? I read about a product designed for this application, it is called Terra Block. Do you know where I can get it? Writing from Victoria, Canada and would appreciated your advice. Thank you, Alfons
I have a 2 story log cabin sitting on top of a concrete block foundation. The property is on a hill, the basement has a dirt floor, presently covered with 6 mil plastic, basement is is 2 different levels, is large, and want to know what would be best to cover the walls with, either eps or polyiso with foil, there is no source of ignition, no furnace or WH, all are on first floor. I was leaning towards polyiso with foil backing, but the eps looks good too!
I have a 1920’s Chicago bungalow with rear addition (built in 60’s) above a previously open storage area which was converted to a crawl space. Insulation under floor which is performing poorly resulting on cold floor and cold addition, the radiant heat can’t keep thermostat temps during cold weather. There is a catch basin in the crawl space for clog prevention of kitchen and laundry waste lines. There is a vent and a exterior doorway. I am on the fence between encapsulating vs. better insulation under the addition floor + maybe plywood with foam spray seal. Also not sure if I need a vent for catch basin if I were to proceed the encapsulation route.
Hi Tim,
We have a 1922 Bungalow in Portland, OR. The crawl space is vented and not insulated. I started installing a white 6 mil vapor barrier on the ground. I have extended it to the top of the concrete foundation which is about 6 inches above the soil. From that point up it is rough sawn 2×4 wood framing.
I was reading through your post and the replies but didn’t see a condition like we have described. I’m assuming that I should insulate the stud cavity before applying the rigid insulation to the crawl space side of the studs. I was thinking that an unfaced fiberglass batt insulation to fill the cavity and then 2 layers of rigid polyiso (for 4 inch thickness) would be a good means to insulate. What do you think of this approach? Should I tape the seams of each layer of the rigid insulation? And caulk the edges of the rigid to the joists, where the rigid fits in between joists at the rim joist.
Hi Tim, I have a house with an addition and it’s own crawl space and HVAC. I am conditioning the 2 crawl spaces. Should the block walls that the 2 spaces have in common get a vapor barrier and/or insulation? Although these are not exterior walls, I am concerned about moisture coming from the ground and through the exposed block. These are also separate HVAC zones and I am concerned about thermal loss.
Tim I have a complicated problem. I’m wondering is there help. We have a crawl space that opens into the unfinished basement. We found out the previous owner dug out the basement. Our crawlspace floor is our basement ceiling. We have been having an ongoing problem with voles burrowing into the crawlspace as well as squirrels. I even caught a rat. The voles get in the crawlspace and now they have gotten in the house. I’m so afraid. I just want to move. A company said they can encapsulate the crawl space but the rodents can bite or burrow through. What should we do?
Hi Jennifer,
Solving your rodent problem will require the services of an experienced pest control contractor. The contractor will need to seal openings that are providing access to your basement & crawl space. Once the pest control contractor has completed his part of the job, you can proceed with encapsulation. Good luck.