Myhomescience.com will be producing a series of energy-upgrade case studies. The first describes a job done in 2013 by Halco Energy. Halco was recently recognized as “best in the country” in a field of over 1,900 Home Performance with ENERGY STAR® contractors nationwide. It is a member of the Dr. Energy Saver network.
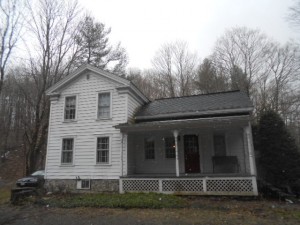
This 1830’s farmhouse was in dire need of energy saving improvements. Now, it’s properly insulated and has been updated with a much more efficient heating system.
Halco Energy and its customers know cold. They live in New York’s Finger Lakes region where average winter lows are below 20° F and often plunge below 0° F.
Last year, a client asked Halco to conduct a home energy audit of their 1830s farmhouse.
“The overall temperature in the house was inconsistent,” said the homeowners. “We were told by Halco that the furnace was to blame — it was too large for the house, so when we cranked it up we’d feel too warm; when it cranked back down, we’d feel too cold. We also had cold areas, especially in the one section of the house that has a crawlspace and not a full basement. The upstairs was also cold. This was mainly due to insufficient insulation.”
Upper New York State
House description:
1700 square foot, 1-1/2 story farmhouse
Start and completion:
May 2013 to July 2013
Challenge:
Upgrade the efficiency and comfort of an 1830’s farmhouse
Solution:
Combine top-to-bottom insulation with geothermal and a high-efficiency backup propane furnace
Project manager: Todd Martin, Halco Renewable Energy
Cost: $54,000 ($35,000 after a $3,000 NYSERDA grant and $16,000 in tax breaks over three years)
Savings: $4,000 annually
Not surprisingly, energy bills were very high — nearly $6,000 per year for a modest-size, 1,700 sq. ft. home. Looking forward to retiring in their home, this was an unsustainable expense for the homeowners.
“This was a case where many solutions needed to be implemented to get the home where it needed to be,” says Todd Martin, Halco project manager.
Because expensive system upgrades rarely make sense without addressing insufficient insulation, Halco upgraded insulation levels throughout the home.
“We addressed the home’s insulation deficiencies completely from top-to-bottom,” says Martin. The Halco installation crew applied 5 in. of high-density spray foam along the attic rafters, under the roof deck, and over the gable walls. In addition, they added 12 in. of cellulose to the attic floor. Cellulose was chosen because of its ability to resist both air movement and heat flow.
Cellulose was also used to insulate the first and second floor exterior walls. In enclosures, such as wall cavities, Halco installers use a technique called “dense packing.” It dramatically reduces air infiltration while providing adequate R-value. The cellulose is shot at high velocity into stud bays through holes in the exterior sheathing. (Typically, some siding must be removed to bore the holes.) The installer builds up layers of firmly packed cellulose until all voids are fully packed. An infrared camera may be used to check for voids during the filling process.
Halco’s crew didn’t stop there. The old crawlspace was a source of cold air in winter. In summer, its high relative humidity was the perfect environment for mold growth, rot fungus, corrosion, and insect infestation. In fact, the homeowners complained of musty odors in their home. Halco felt that the best solution was to encapsulate and insulate the crawlspace. TerraBlock, a ¾-in. thick insulating pad, was used to seal and cover the floors. It in turn was covered by a 20 mil. CleanSpace polyethylene vapor barrier. Crawlspace walls were then sealed with 2 in. of spray foam insulation from the ground up to and including the box sills and rim joists. Spray foam was also applied to the stone walls in the basement portion of the house.
Moist warm air infiltration, that had made the home difficult to cool on hot, humid days, has been dramatically reduced. “The other benefit is the lack of mildew,” say the homeowners. “We were always fighting that in the summer time. Now, the house is dry and “normal” in the summer. There is no annoying mildew smell.”
Goodbye to outdated HVAC equipment
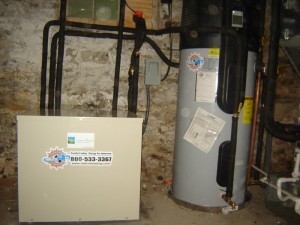
A new Earthlinked geothermal heat pump with a desuperheater inside combine with a new water heater to provide heat and hot water.

The new propane furnace is rated at 95% efficiency. It automatically comes on only when the geothermal heat pump cannot handle the home’s heating load.
The most dramatic improvement made by Halco was the installation of a geothermal heating system to meet most of the space- and water-heating needs. The bulky old 70-percent-efficient oil furnace, its accompanying oil tank, and the old hot water heater were replaced with a new 3-ton Earthlinked geothermal heat pump, a desuperheater water heater, and a new water heater tank. Geothermal heat pump systems draw heat from the ground instead of the air like conventional “air-to-air” heat pumps.
In direct exchange geothermal systems, such as this one, “wells” are bored into the earth and refrigerant piping is installed in the holes. (This home required 3 100-ft. wells.) The refrigerant delivers heat that is ever-present in the earth to the heat pump, which uses it to produce hot air for distribution throughout the house. In summer, a reversing value may be used to reverse the process and draw heat from (cool) the home. The unwanted heat is either returned to the earth and/or used to heat domestic water.
In addition, the heat pump is equipped with a desuperheater so it can be used to heat water for washing. A desuperheater is a small, secondary heat exchanger installed inside the heat pump. It transfers heat from the heat pump’s compressor to domestic water. The heated water is then stored in a hot water tank until it’s needed.
Halco also installed a 95% efficient 45,000 BTU, Goodman 2-stage propane furnace to act as the air handler (blower that moves heated air throughout the house) and as a backup heating system. To help manage the load of this new setup, the home’s existing electrical service was upgraded to a 200 amps. In addition, Halco installed a 7kW Generac back-up generator to keep the systems running during power outages.
“The results of the improvements we made on this home will be felt for years to come. The new geothermal heat pump, propane furnace and desuperheated water heater are much more efficient than the home’s prior systems. In addition, by air sealing and insulating the attic, exterior walls and crawl space, we minimized the amount of conditioned air leakage–which translates to less drafts, consistent room temperatures and increased comfort,” says Martin.
Perhaps the most dramatic result of the improvements, however, is the annual savings on energy bills and the relatively fast payback. “After completing all of the work, they are expected to see an energy savings of about $4000 per year,” says Martin. After eight months, the homeowners say, Martin’s projection is proving accurate. Electricity costs have risen, but the increase is more than offset by fuel costs that are running 80 percent less than prior years during an unusually cold winter.
How much did this whole project cost?